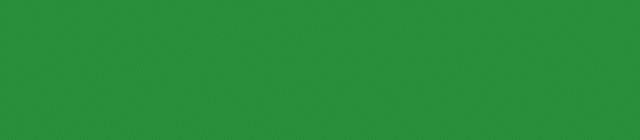
18650是指电池的外形规格,其中: 18表示直径为18mm,65表示长度为65mm,0表示圆柱形电池,是最早、最成熟、最稳定的锂离子电池型号,其具有制造自动化水平高、电池一致性好、单体能量密度高、散热性好等优点。以18650圆柱形锂离子电池为例,揭示锂电池制造工艺流程,分析各流程的管控要点及其对电池电性能的影响,为锂离子电池应用提供重要的参考。
一、锂离子电池
1. 1 锂离子电池工作原理
锂离子电池主要由正极、负极、隔膜和电解液组成,依靠Li+在正极和负极之间移动来工作。充电时Li+从正极脱嵌,经过电解质嵌入负极,负极处于富锂状态; 放电时则相反。以钴酸锂为正极,石墨为负极的锂电池为例,充电时的化学反应公式如下:
1. 2 锂离子电池结构
锂离子电池主要由正极、负极、膈膜和电解液四大主材组成。同时,一颗完整的18650圆柱形锂离子电芯还包括正负极引线、上下绝缘片、盖板及外钢壳等辅材,其结构如图1所示。
图1 18650圆柱形锂离子电池结构
二、锂离子电池制造工艺与管控点
锂离子电池的制造工艺复杂,工序众多,任何一个环节出现失误都将影响锂离子电芯的性能或带来安全问题,因此,只有严格管控每一道制造工序,才能制造出性能优异和安全有保障的合格电芯。文中以18650圆柱形锂离子电池为例,详细介绍电池的制造工艺并说明每一道制造工序的管控要点及其影响,并将制造工序分为制造前段、制造后段及筛选工艺3个阶段,依次阐述,如图2所示。
图2 锂离子电池制造工序
2. 1 锂离子电池制造前段工艺与管控点
电池制造前段工艺包括合浆、涂布、辊压、分切、制片、卷绕、入壳、底焊、辊槽及烘烤10道工序,前段工序的核心是将粉末状的正负极材料制作成一颗卷芯。
合浆工序是指正极或负极粉末、导电剂及黏接剂按一定比例均匀混合成悬浊浆料,再将浆料通过涂布机在集流体表面涂覆一层厚度均匀的涂层,即涂布工序。涂布完成后,极片需通过辊压机调整轧辊间隙、收放卷位置、张力等,并用试片试压,确保试压后的试片厚度符合工艺参数要求。再用分切机分切成单颗电芯所需要的宽度,最后在制片机上焊接极耳并在极耳位置贴上绝缘胶包覆裸露的集流体和极耳,至此,正负极片的制作结束。
合浆工序最主要的工艺管控点在于环境的湿度控制,因为水分是锂离子电池生产过程中需要严格控制的关键指标,环境湿度较大、水性黏结剂的使用等因素都会导致极片制备过程中水分含量的增加; 分切工序需重点管控极片边缘裁切毛刺大小,且不能出现明显的掉料情况,否则极片因掉料或毛刺太大而刺穿隔膜,造成短路; 制片工序应防止极耳虚焊、偏焊、漏焊或极片掉料及绝缘胶偏贴或漏贴等; 卷绕工序是圆柱形锂电池成形的重要工艺,由条状形正负极极片和隔膜通过卷绕机卷成圆柱形卷芯,这一工序管控要点在于负极极片必须完全包覆正极极片,而隔膜必须完全包覆负极极片,对工艺精度的要求非常高。如果负极未充分包覆正极,则充电过程中隔膜上有析锂现象发生,随着析锂程度加重导致正负极接触短路,由于锂枝晶导致的内短路事故是电池失效的重要形式,可能引起起火爆炸等事故。如果隔膜未包覆负极,直接导致正负极接触,电芯短路,造成严重安全事故。
卷芯完成后需放入钢壳并通过底焊使得负极耳与钢壳连接,这时整个钢壳就是电池的负极,再通过辊槽固定钢壳内的卷芯。入壳与辊槽工序不能破坏卷芯,辊槽高度需严格把控,过低时,卷芯被破坏; 过高时,卷芯容易松动。最后将已入壳的卷芯置于烘烤箱中烘烤,直至卷芯的水分含量达到标准后才能转入下一工序。烘烤是为了严控卷芯的水分含量,是至关重要的一步。
2. 2 锂离子电池制造后段工艺与管控点
电池制造后段工艺包括注液、焊接、封口、清洗及套膜。注液即通过注液机将电解液注入烘烤后水分要求合格的卷芯,注液完成后,锂电池的四大主材均被应用到电芯之中,注液工序关键在于精控注液量、控湿控温及防水,且需达到电解液能够较好地浸润渗透到正负极极片的效果。电解液量的多少直接关系着电池的安全性能和容量,如果注液量过多,电池内部产气量较大,圆柱形电池的安全阀往往会过早开启; 如果注液量过少,电池容量会偏低而且析锂,更容易产生热失控甚至引起爆炸。再将盖板与正极耳焊接在一起,这时整个盖板就是电池的正极,焊接的管控点在于防止虚焊、偏焊及盖帽外观不良。
下一道工序就是封口,封口是将钢壳与盖板密封,将整个卷芯与外部环境隔离,整个卷芯就是一个密闭的电化学系统。封口工序是整个电芯制造最后一道至关重要的工序,其压力成形技术的工艺稳定性决定了电池的密封性是否完好、可靠。完成封口工序意味着一颗外形完整的电芯制造已经全部结束。清洗工序的目的是清除电池钢壳表面残留的电解液,防止电解液腐蚀钢壳,而套膜工序是保证电芯正负极端分开,防止外部电路发生短路,同时使电池有一定的美观度,这两道工序还需要对外观不良电池进行筛选。
2. 3 锂离子电池筛选工艺与管控点
由于电池原材料、生产工艺等差别,电池容量、电压、内阻等性能存在差异,使得电池组性能达不到单体电池水平,使用寿命远短于单体电池,影响电动汽车的使用。电池筛选工艺包括活化、化成、陈化、分选及分容工序。
SEI 膜是锂离子电池能够长期稳定工作的保障条件,对其容量、倍率、循环、安全性能等都有至关重要的影响。选择合适的化成电流、化成电压、化成温度等,对优化和提高电池性能有非常重要的作用,故而这一工序十分重要,实际操作过程中需防止电池反接、过充及接触不良等。
陈化工序是将某一荷电状态下的电芯在一定恒温环境中搁置一段时间,通过测试前与测试后的电压进行数据筛选,剔除压降大或压降异常的电芯。一般电芯内部发生微短路或存在剧烈副反应时,电芯压降会较大,反映出电芯性能差会有一定的安全风险,因此,压降是电芯筛选的重要参考指标之一。
由于常温老化用时较长,为了缩短生产周期,绝大多数锂离子电池厂家采取的是高温或高荷电态老化方式,工艺管控要点需密切监控搁置过程中有无异常情况发生,并及时采取行动确保安全,因为一般高温老化房是个密闭空间,初始阶段不易被及时发现,一旦发生火灾,后果不堪设想。
分选工序是根据电芯交流内阻大小分选出不同内阻档位电芯,剔除内阻异常电芯,易于选取合适的电芯串联或并联搭配,因此,内阻也是电芯筛选的重要参考指标之一。
分容工序即测定电芯容量后按不同容量档位筛选电芯,剔除容量不合格电芯,由于容量与温度关系较大,分容时的环境温度控制越精准,容量越接近真实值,档位分配更准确,因此,温度控制是分容的管控要点。出货电芯必须是经过压降、内阻及容量筛选且合格的电芯。(来源:锂电联盟会长)

课程推荐

就业推荐
点它,分享点赞在看都在这里
原文始发于微信公众号(电池联盟cbcu):18650电池制造工艺与关键点!
新能源汽车的快速发展带动了动力电池的高速增长。动力电池生产流程一般可以分为前段、中段和后段三个部分。其中,前段工序包括配料、搅拌、涂布、辊压、分切等,中段工序包括卷绕/叠片、封装、烘干、注液、封口、清洗等,后段主要为化成、分容、PACK等。材料方面主要有正负极材料,隔膜,电解液,集流体,电池包相关的结构胶,缓存,阻燃,隔热,外壳结构材料等材料。 为了更好促进行业人士交流,艾邦搭建有锂电池产业链上下游交流平台,覆盖全产业链,从主机厂,到电池包厂商,正负极材料,隔膜,铝塑膜等企业以及各个工艺过程中的设备厂商,欢迎申请加入。
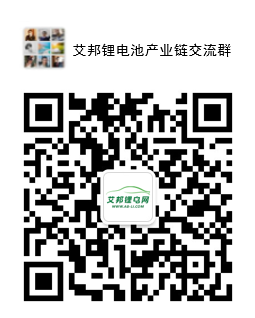
长按识别二维码关注公众号,点击下方菜单栏左侧“微信群”,申请加入群聊