(二)告警和保护
保护即安全管理,在电池出现异常状态时,BMS要向平台进行告警并进行保护电池。
BMS通过监测,会对异常参数发出不同类别的异常告警,并采取相应的处理措施。同时,会将异常告警信息发送至监控管理平台并生成不同等级的告警信息(一级告警、二级告警、三级告警)。比如,温度过热时,BMS会直接断开充放电回路,进行过热保护,并向后台发出告警。
锂电池主要的告警和保护有:
过充:单体过压、总电压过压、充电过流;
过放:单体欠压、总电压欠压、放电过流;
温度:电芯温度过高、环境温度过高、MOS温度过高、电芯温度过低、环境温度过低。
状态:水浸、碰撞、倒置等。
(三)均衡管理
均衡管理的必要性来自于电池的不一致性,可分为两类:
一类是生产的不一致性
一类是使用的不一致性
从生产上来看,即使是同一厂家同一批次生产的电池,也都有自己的生命周期、自己的“个性”——每个电池的容量不可能完全一致。在生产过程中,由于隔膜、阴极、阳极等材料的不一致,造成整体电池容量的不一致。比如组成一个48V/20AH电池组的各电芯,其压差、内阻等的一致性指标,均有一定范围内的差异。
从使用上来看,在电池充放电的过程中,即使两个电芯的生产加工一模一样,但是在电化学反应的过程中是永远不可能一致的。比如对于同一个电池包,处于不同位置的电芯,其温度和磕碰度就不一致,这就造成充电量、放电量的长久不一致,从而导致电芯容量不一致。
电路状态 |
MOS1 |
MOS2 |
充放电状态 |
正常状态 |
通 |
通 |
可充可放 |
过充保护 |
通 |
关 |
可放不可充 |
过放保护 |
关 |
通 |
可充不可放 |
过流保护 |
关 |
通 |
过流解除时,可充放 |
短路保护 |
关 |
通 |
短路解除时,可充放 |
(二)二级保护电路:三端熔丝Fuse
为提升安全性,在AFE保护失效时,需要增加一个二级保护,也就是说在一级软件关断的基础上,需要增加二级物理熔断保护机制。目前,应用最多的就是REP(Resistor Embedded Protector,内置电阻保护器),性价比较好的就是带加热的三端熔丝Fuse,如下图所示:
当电流过大时,和普通的熔丝原理一样会被动熔断;当检测到MOS运行状态异常时,主控控制三端熔丝主动熔断。
三端熔丝的优点非常突出,阻抗小功耗小,设计简单,速度快,保护效果好,已大量应用在电动车、储能、手机等所用锂电池BMS上。
(三)三级保护电路: NTC和TVS
1.NTC热敏电阻
热敏电阻也称半导体热敏电阻器, 其电阻值对温度极为敏感,随温度的变化有极为显著的变化,它与一般的固定电阻不同,属于可变电阻的一类,广泛应用于各种电子元器件中。热敏电阻可分为PTC和NTC两种。
PTC(Positive Temperature Coefficient,正温度系数热敏电阻器)在温度越高时电阻值越大,以电路阻断形成温度保护。PTC主要用于发热原件、温度控制保护等,如灭蚊器,暖风机。
NTC(Negative Temperature Coefficient,负温度系数热敏电阻器)在温度越高时电阻值越低,主要用作电阻温度传感器和限流装置。
锂电池BMS一般使用NTC,其耗电量极少,在很大的温度范围内(-40~125℃)具有非常出色的精确性,而且对温度变化的反应很迅速,主要有三大作用:
(1)温度测量
可以利用NTC的电阻值随着温度上升而下降的特性,通过测量电阻值来确定相应的温度,从而达到检测和控制温度的目的。
在实践中,可以通过NTC来实现以下三个温度的测量:
电芯温度:将NTC热敏电阻放置在电芯之间,实现电芯温度的测量。当然这个要考虑每个NTC所覆盖的电芯数量,在测量准确性和经济性之间取得平衡。
功率温度:将NTC热敏电阻放置在MOS之间,实现功率温度的测量。安装时NTC要与MOS器件紧密接触,以确保数据的准确。
环境温度:将NTC热敏电阻放置在BMS板上,实现环境温度的测量。安装位置应远离BMS板上的功率器件,以避免误报。
以上三个温度通过AFE汇集到MCU后进行计算和管控。
(2)温度补偿
在各种交直流电路中,大部分的元器件都具有正温度系数特性,即电阻值随温度的上升而增大,这时就需要使用负的温度系数热敏电阻(NTC)进行补偿。一正一负,正好可以抵消由于温度变化所产生的误差,提高精度。
(3)抑制浪涌电流
浪涌(electrical surge),也叫突波,即瞬间出现超出稳定值的峰值,包括浪涌电压和浪涌电流。
电子电路在开机的瞬间会产生很大的浪涌电流,这一瞬间的冲击电流可能损坏MOS、保险丝等器件。将NTC串联到回路中,可以有效的抑制浪涌电流。在电源接通前,因为温度较低,NTC具有较大的电阻(通常在6-12欧姆左右),可以抑制电流;之后随着充电的继续进行,温度逐步升高,NTC的电阻逐渐下降(大约为0.5-1欧姆左右),电流逐步抬升,不影响电路工作。
但正常工作时,NTC已低阻,对于突发的浪涌电流,就起不到保护作用了,所以NTC抑制浪涌电流主要是开机阶段。
这时,对于浪涌的保护就需要用到TVS。
2.TVS瞬态电压抑制器
TVS(Transient Voltage Suppressors)即瞬态电压抑制器,响应速度特别快,主要用来端口防护,防止端口瞬间的电压冲击造成后级电路的损坏。如下图所示:
当电路出现异常高电压时,TVS会迅速由高电阻状态突变为低电阻状态,将瞬时过电流释放到地,并将异常过电压控制在较低的水平,从而保护后级电路免遭损坏。当异常过电压消失后,TVS阻值又恢复为高阻态。
三、BMS关键器件的国产化
目前,国内BMS生产制造中,缺口最大的就是相关核心芯片,尤其是AFE芯片。宁德时代董事长曾毓群曾表示,宁德时代在电池生产过程中没有直接涉及美国的技术、材料或是设备,现在唯一依赖美国的就是BMS里的芯片。
近两年,由于国外芯片缺货以及厂商供货周期的延长,使得国内的供应商获得更多供货机会和产品验证机会。
(一)AFE模拟前端芯片
从AFE的生产厂家来看,美国厂商占据全球接近70%的市场份额,美国的ADI(亚德诺半导体)和TI(德州仪器)共占有大约60%的市场份额。欧系厂商ST(意法半导体)、NXP(荷兰恩智浦半导体)和Ams AG(奥地利艾迈斯半导体)也占据重要地位。近年来,我国的中颖电子、芯海科技、思瑞浦等上升也比较快。
(二)MCU芯片
从生产厂家来看,MCU主要为欧美、日本和台湾地区企业占据,仅NXP(荷兰恩智浦)、Microchip(美国微芯科技)、ST(意法半导体)、infineon(德国英飞凌)就占据超80%的份额,TI(德州仪器)、Nuvoton(中国台湾新唐科技)、ROHM(日本罗姆半导体)、三星、东芝五家企业占据11.4%,而中国大陆企业所占份额6.5%不到。
目前,中国本土的GD(兆易创新)、极海半导体等成长也很快。
四、BMS问题及优化方向
BMS不只是BMS研发厂家的职责,它是一个系统工程,需要电芯厂家、BMS厂家、PACK厂家,尤其是换电运营商的共同参与。
(一)换电运营商
BMS作为锂电池的管理控制系统,实质是将基于用户需求的运营经验,进行细化、总结、固化到BMS中。而换电运营商其最接近用户,最懂用户的需求,因此,换电运营商是BMS的主导者。
(二)BMS厂家
BMS厂家最懂电子电路,它基于电芯性能,结合换电运营商需求,进行BMS架构搭建和开发,起着承上启下的作用。但其弱点也非常突出,主要表现在对电芯的理解深度还不够理想,导致管控策略和电芯实际存在差异。
(三)电芯厂家
电芯厂家最懂化学,这其实是整个BMS管控的基础所在,因为BMS的一切管控都是基于电芯和电池组进行的。但目前,电芯厂家对电子电路的理解还需要提升,比如哪种信息采集方式可以采集到最准确的电芯信息。
(四)PACK厂家
PACK厂家是将电芯与BMS组装成电池组,其对电芯的排列、BMS位置的摆放和组装的加工工艺等都影响着BMS功能实现的程度和准确性。PACK厂家需要根据换电运营商的要求,从产品质量出发,以最后把关的视角对电芯和BMS厂家提出相关要求。
因此,BMS保护逻辑的设计是运营经验的积累和固化,而保护逻辑的有效落地需要以电芯为基础的电路设计以及产品性价比的提升。电芯厂家、BMS厂家、PACK厂家要在换电运营商的主导下,既做好本职专业,又做好相互协同,形成BMS产品系统集成的合力,而这将是今后BMS发展和问题解决的必由之路。
原文始发于微信公众号(遇见新能源):浅析BMS保护机制及工作原理
新能源汽车的快速发展带动了动力电池的高速增长。动力电池生产流程一般可以分为前段、中段和后段三个部分。其中,前段工序包括配料、搅拌、涂布、辊压、分切等,中段工序包括卷绕/叠片、封装、烘干、注液、封口、清洗等,后段主要为化成、分容、PACK等。材料方面主要有正负极材料,隔膜,电解液,集流体,电池包相关的结构胶,缓存,阻燃,隔热,外壳结构材料等材料。 为了更好促进行业人士交流,艾邦搭建有锂电池产业链上下游交流平台,覆盖全产业链,从主机厂,到电池包厂商,正负极材料,隔膜,铝塑膜等企业以及各个工艺过程中的设备厂商,欢迎申请加入。
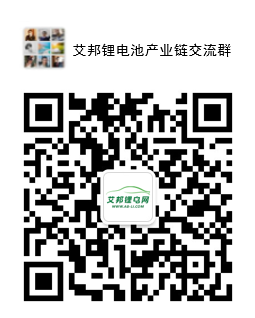
长按识别二维码关注公众号,点击下方菜单栏左侧“微信群”,申请加入群聊