内容 | 廖华星
编辑 | 康佳丽
锂电池是20世纪开发成功的新型高能电池,可以理解为含有锂元素(包括金属锂、锂合金、锂离子、锂聚合物)的电池,可分为锂金属电池(极少的生产和使用)和锂离子电池(现今大量使用)。
锂离子电池具有能量高、电池电压高、工作温度范围宽、贮存寿命长等优点,已广泛应用于军事和民用小型电器中,如移动电话、便携式计算机、摄像机、照相机等。
锂离子电池的主要组成:
(1)正极——活性物质主要指钴酸锂、锰酸锂、磷酸铁锂、镍酸锂、镍钴锰酸锂等,导电集流体一般使用厚度在10--20微米的铝箔;
(2)隔膜——一种特殊的塑料膜,可以让锂离子通过,但却是电子的绝缘体,目前主要有PE和PP两种及其组合。还有一类无机固体隔膜,如氧化铝隔膜涂层就是一种无机固体隔膜;
(3)负极——活性物质主要指石墨、钛酸锂、或近似石墨结构的碳材料,导电集流体一般使用厚度在7-15微米的铜箔;
(4)电解液——一般为有机体系,如溶解有六氟磷酸锂的碳酸酯类溶剂,另有些聚合物电池使用凝胶状电解液;
(5)电池外壳——主要分为硬壳(钢壳、铝壳、镀镍铁壳等)和软包(铝塑膜)两种 。
01
铜箔是锂离子电池的重要基础材料,主要应用于电池负极,其作用是将电池活性物质产生的电流汇集起来,以产生更大的输出电流。
铜箔由于导电性好、良好的机械加工性能、质地较软、制造技术较成熟成本优势突出等特点,成为锂离子电池负极集流体的首选。
铜箔是影响锂电池比能量和成本的关键材料。
质量方面,铜箔约占电池质量的9%,是仅次于正极、负极、电解液的关键材料,影响电池的能量密度。
成本方面,铜箔成本占磷酸铁锂电池成本的8%,是影响电池成本的重要材料之一。
02
锂电铜箔根据组成材料的不同可分为传统铜箔与复合铜箔(目前主要方向为PET铜箔)。
动力电池高能量密度、高安全性发展方向趋势明确,铜箔超轻薄化可有效提升电池能量密度。
在相同体积的锂离子电池中,铜箔的厚度越薄,其承载负极活性物质的能力越好,电池的容量越大、对电池的能量密度提升作用越大。
故高密度、低轮廓、超轻薄化、高抗拉强度、高延伸率是锂电铜箔的重要发展趋势。
PET铜箔主要优势:
(1)高安全性∶一方面,复合铜箔导电层较薄,发生局部短路时更容易被熔断,致使局部电流被切断,降低因短路产生的热量。
另一方面,复合铜箔的基膜为高分子材料,不具备导电性,且具有较大的电阻,能够减少短路电流,提高电池的安全性。
(2)高能量密度∶中间层采用轻量化高分子材料,重量比纯金属集流体降低50%-80%,电池能量密度实现提升5%-10%。
(3)长寿命∶高分子材料相比金属具有低弹性模量,电池的循环寿命实现提升5%。
(4)强兼容∶将传统集流体直接升级为复合集流体不影响电池内部电化学反应,能够直接运用于各种规格、不同体系的动力电池。
(5)低成本:传统铜箔原材料成本占比达83%,而PET铜箔理论上单位材料的铜用量仅有传统箔的1/3左右。
但目前复合铜箔的加工成本因处于制造初期成本比较高,叠加工艺不成熟导致良率相对不高,目前价格还没有传统铜箔低。
03
由于PET表面光滑的特性,增强铜层与PET薄膜的结合力以及使得采用水电镀加厚的铜层具有均匀性和平整性是其技术。
PET复合工艺流程图
目前PET铜箔制作过程主要包括两步法和三步法:
两步法
复合铜箔两步法生产步骤包括磁控溅射和水电镀。
首先,采用磁控溅射真空镀膜技术对基础材料表面进行金属化处理,确保材料导电以及膜层的致密度和结合力,之后通过水电镀将铜层增厚。
三步法
三步法生产步骤包括磁控溅射、真空镀膜和水电镀。
第一步仍是采用磁控溅射技术,以铜作为靶材,在PET基膜上进行纳米涂层,使PET基膜表面沉积铜层。但相较于两步法,三步法磁控溅射环节要求的铜膜厚度更低,因此线速度会相应提高。
第二步是采用真空蒸镀技术,对应的设备为蒸镀机。蒸镀机器内包括蒸镀室和卷取室,在高真空下加热金属,使其均匀地蒸发镀在薄膜表面。
第三步是采用电镀增厚铜层至1μm左右,实现集流体导电需求。
无论采用两步法还是三步法,磁控溅射和水电镀都是不可或缺的步骤。
04
对PET材料进行电镀工艺前,需要先进行磁控溅射,这是由于PET高分子材料本身为绝缘体,无法进行直接电镀,需要在其表面通过磁控溅射形成薄金属层,使基膜材料导电。
磁控溅射工艺优势在于能够使得铜和基膜材料结合较好,但目前工艺难点在于过程中需要使用高压放电,可能存在膜穿孔现象。
此外一次磁控溅射只能够形成十几纳米的金属层,1μm的铜层需要20-30次的溅射,效率较低。
真空磁控溅射是制备薄膜的主要技术之一,下游应用广泛。通过电场和磁场的作用,工作气体产生辉光放电,离子轰击靶材溅射出材料粒子形成薄膜,目的是在塑料薄膜表面制作一层金属层、使非金属材料金属化。
真空磁控溅射具有镀膜稳定性好、重复性高、均匀度好、适合大面积镀膜、膜层致密、结合力好、工艺灵活度高等优点。
05
塑料薄膜在经过真空磁控溅射附着金属层后,采用水介质电镀的方式,将铜层加厚到1μm,即可制成复合铜箔。
PET镀铜技术来源于PCB电镀,但相比于PCB电镀,PET镀铜的基材更薄(PCB最薄板厚24μm,PET膜厚20-80nm)、张力控制难度较大、均匀性要求更高。
设备研发难点在于在膜很薄的情况下需要满足膜材料厂商对PET复合膜材不变形、均匀度好、无穿孔的要求,且水平镀铜技术难度大于PCB镀铜。
06
根据调研数据,1GWh对应复合铜箔需要采用两台真空镀,三台电镀铜设备,价值量约5500万,其他假设如下:
①据GGII,EVTanK等预测,2022-2025年储能电池以及动力电池需求共为717GWh、991GWh、1341GWh、1734GWh;
②假设PET铜箔渗透率2025年能提升至20%;
③假设2021年单台磁控溅射设备价值量为1000万,单台电镀设备价值量为800万。随着机器设备改进,熟练程度增加,设备利用率能从65%提升到70%。
随着PET镀铜渗透率逐年提升,2022至2025年磁控溅射设备新增市场空间分别为13亿、24亿、28亿以及36亿元,电镀设备市场空间分别为13亿、22亿、21亿及24亿元。
PET铜箔市场空间,假设售价6元/平,2022至2025年对应市场空间18、60、120、210亿元,复合增速84.81%。
07
1、上游设备
上游设备主要以磁控溅射设备+水电镀设备为主,其中磁控溅射设备(PVD)目前国际市场主要被应用材料、爱发科、德国菜宝等跨国公司占据,我国真空设备制造近年来发展迅速、国产替代趋势明显,主要企业包括宏大真空、汇成真空、振华科技、广东腾胜等。
复合铜箔方面,广东腾胜率先研制出量产型真空镀膜设备,并已应用至重庆金美、日本TDK等下游客户。
国内镀铜设备竞争较为充分,但目前仅东威科技能量产PET镀铜设备,截至2021年底,东威科技卷式水平镀铜线两代产品均已实现量产,双边夹具导电超薄卷式水平镀铜线通过试验机完成预设计目标,先发优势突出。
2018-2021年东威科技营收从4.07亿元增长至8.05亿元,归母净利润从0.63亿元增长至1.61亿元,业绩稳定增长。2022年H1公司营收4.12亿元,同比增长17.86%,归母净利润0.93亿元,同比增长34.38%。
据公司2021年年报披露,公司卷式水平膜材电镀设备贡献965.66万元的营业收入,随着PET复合铜箔在锂电行业的需求扩大,公司作为早期布局PET铜箔电镀设备的龙头企业,产能有望加速释放,为公司发展贡献新增长极。
2、中游生产商
新能源行业和储能行业快速发展对锂电池负极材料提出了更高的要求。
相较于传统锂电铜箔,PET铜箔具备安全性高、能量密度高、寿命长等诸多优势,未来有望替代部分传统锂电铜箔,实现规模化应用。
目前国内相关企业正加速布局复合铜箔领域,包括双星新材、万顺新材、诺德股份、阿石创、宝明科技等,有望推进产业化进程。
目前行业进展最快的上市公司中,如双星新材已经向客户送样。
欢迎关注:
专注新经济,拥抱星辰大海,捕捉人类之光。
原文始发于微信公众号(浩宇观点):PET铜箔:放量在即,未来可期!
新能源汽车的快速发展带动了动力电池的高速增长。动力电池生产流程一般可以分为前段、中段和后段三个部分。其中,前段工序包括配料、搅拌、涂布、辊压、分切等,中段工序包括卷绕/叠片、封装、烘干、注液、封口、清洗等,后段主要为化成、分容、PACK等。材料方面主要有正负极材料,隔膜,电解液,集流体,电池包相关的结构胶,缓存,阻燃,隔热,外壳结构材料等材料。 为了更好促进行业人士交流,艾邦搭建有锂电池产业链上下游交流平台,覆盖全产业链,从主机厂,到电池包厂商,正负极材料,隔膜,铝塑膜等企业以及各个工艺过程中的设备厂商,欢迎申请加入。
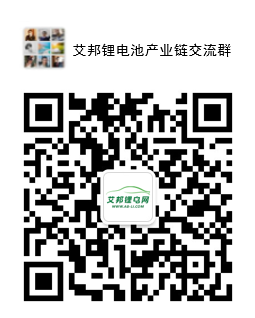
长按识别二维码关注公众号,点击下方菜单栏左侧“微信群”,申请加入群聊