《电子铜箔资讯》编者按
向业界推荐一篇好文。
本文对一类新问世的锂电池负极集流体用“复合铜箔"产品及其产业的发展前景做了深入细致的分析。文章所提出的问题,很有参考价值,也带给我们更多的深层思考。此文观点仅代表作者个人。
出于有助于我国锂电池用电解铜箔及复合铜箔产业及市场的发展,中电材协电子铜箔材料分会秘书处很提倡对此论题有各种不同看法、观点的更多论文发表。
“复合铜箔”替代“电解铜箔”在锂离子电池中的应用概念在市场上宣传已有数年,尤其到今年达到一个前所未有的高度,今年10月,XX锂电产业网在深圳“胜利举办了动力电池复合铜箔大会”,把复合铜箔“应用前景”推到新高,所公布的“信息”引起电子铜箔行业内外的相关利益群体惴惴不安,仿佛在短期内就可以实现在锂电池行业大规模应用,这样“场景”会产生吗?为此本人就“复合铜箔”的前世、今生与未来做一粗略的研究、分析,供产业链同仁参考,起稳定既有行业次序的作用。
1.复合铜箔“前世” 1.1 挠性覆铜板生产与命名规则 覆铜板有七种分类方法,其中按机械刚性划分为刚性与挠性覆铜板(也可以称为:柔性覆铜板)。挠性覆铜板具有良好的耐折性能,使之在便携电子产品中大规模的应用,挠性覆铜板有两种生产工艺,一种是两层法,另一种是三层法。两层法有两种工艺路线,第一种工艺路线为在绝缘基材上真空镀膜(真空蒸镀、磁控溅射镀、等离子镀、分子束外延镀、激光镀等几种),形成铜箔层或基础铜导电层,如形成的铜层厚度满足目标厚度指标,则无须电解液加厚电镀,反之则需进行加厚电镀;另一种工艺系在铜箔毛面刷涂PI胶(或其他种类胶),固化后则成柔性FCCL,该工艺与涂树脂铜箔(RCC)工艺类似,只是绝缘基材不同而已。三层法生产工艺由金属箔、绝缘介质基片,中间用不同类型的胶粘剂经过热压粘接而成,系主流FCCL生产方法。
不管是哪种方式生产的FCCL,其结构显示为金属与非金属组成的复合材料,故一般FCCL中文命名为:XX基X层挠性覆铜(其他金属亦可)板,如PI基单层挠性覆铜板。该命名较为正规,符合复合材料命名通用规则,让人一目了然。
1.2金属箔的命名规则
金属箔标识(命名)起源于印制线路用金属箔(IPC4562标准)标准,该标准对各类金属箔标识(命名)进行规范,旧版电解铜箔国标(GBT5230,2020年前标准)对其参照使用,使用时去除其他种类金属箔,新版电解铜箔国标(GBT5230,2020年标准)在旧版国标基础上,进一步去除压延铜箔种类,仅纳入5个电解铜箔型号进行规范;对照IPC印制电路用金属箔标准、不同版本中国电解铜箔国家标准,本人认为IPC标准对金属箔材标识(命名)更具有规范性、全面性,故此列出金属箔标识(命名)规则:
规格单号;金属类型;工艺类型;箔型号;箔厚度;表面处理;轮廓度;质量等级。
标识(命名)依序有8个部分组成,可以覆盖既有印制线路用金属箔品种及其即将诞生品种标识(命名),从标识(命名)8个分项内容来看,其并未列入绝缘基材组成项,故此我们可以理解为:印制线路用金属箔就是以电解、压延工艺生产的,具有不同物理特性(如延伸率、抗拉强度、抗曲绕、粗糙度、厚度)、耐化学特性(耐储存与高温氧化能力)、质量进行分级的单一金属为主金属箔。
1.3“复合铜箔”名称的由来
复合铜箔早期来源于“复合铜箔膜”,在上世纪末我国电缆材料工业出现,其由铜箔、聚酯膜、粘结剂组成,裁成目标宽度卷材,缠绕到通信电缆内层,起到信缆电磁屏蔽防止信号传输失真作用,目前我国电缆材料企业已就该产品申请多个发明专利与实用新型专利,从此诞生了我国最早 “复合铜箔”产业。
1.4不同内含的“复合铜箔”
随着我国PCB、LED、CCL、FCCL、锂电池、阻根材料产业的快速发展,为解决原材料来源多样化、低成本化问题,上述产业逐渐开发、发明出不同技术路线、不同技术指标、不同应用领域的都以“复合铜箔”命名的产品,以满足目标领域的产品使用,目前我们看到除锂离子电池产业外,这些类“复合铜箔”均已工业化生产、使用,可谓是铜加工品内单一名称内含最为丰富的产品。
1.5锂离子电池集流体用“复合铜箔”
早在本世纪初,锂离子电池产业就在锂电池制造专利中出现复合铜箔应用概念,为此掀开了锂电池产业负极集流体用“复合铜箔”(或PET铜箔等)关注热潮,众多发明者参照早期FCCL两层法制造工艺,申请近数百项发明、实用新型专利,与此同时锂电池企业申请了涉及锂电池负极集流体使用“复合铜箔”专利数千项,可谓“成果累累”。
1.6企业、地方、行业、国家标准目前仍是空白
查询锂离子电池用“复合铜箔”、“PET铜箔”国家、行业、地方乃至企业标准,均无所获,仅能查询部分产品质量特性技术指标值。
根据上述“复合铜箔”前世考究,我们大致总结如下:
(1)“复合铜箔”是复合材料,按PCB产业链分工,应该属于FCCL行业;
(2)“复合铜箔”命名存在瑕疵:基于金属箔、铜箔、铜及其合金材料的标识(命名)规则,应该命名为XX基材双面挠性覆铜板,当然也可以参照“背胶铜箔”命名为“XX基双面复合铜箔”,但按PCB产业链传统来讲,“背胶铜箔”属于FCCL行业;
(3)各级产品质量标准基本处于空白状态,生产商、使用(试用)商处于无标可依状态,无法对产品质量进行有效的约束,大规模生产、使用难以产生。
2.复合铜箔生产、使用的技术经济难点
2.1生产端面临技术、质量难点
“复合铜箔”类比FCCL两层法进行制造,其第一步的导电层制造主要采用真空磁控制溅射工艺,第二部铜加厚层采用类似于电解铜箔表面处理工艺,两个步骤虽有参考,可以借助于类似工程、工艺经验,但目标产品“复合铜箔”在衡量指标上与借助工艺生产的产品大相径庭,故此,应该对两个步骤质量“使命”要进行特殊“定义”与分析,基于已选工艺与设备,我们分析认为目前“复合铜箔”试制存在以下主要的技术、质量、成本难点。
(1)基材质量控制与“预处理”
目前业界报到可用多种高分子薄膜作为复合铜箔基材,据已知消息,PET膜选择最为热衷,最薄厚度已经到4μm以下。
从真空溅射原理上认知,基材膜上下表面质量瑕疵、全表面张力均一性、膜本身的物理特性等,都将对真空磁控制溅射铜层(导电层)质量形成产生影响,故此应该建立严格PET原材料质量标准,但到现在为止尚未有基材质量控制标准报道(可能还在试用与商讨中);再有即便形成质量控制标准,供给的PET膜质量可能还是难以达到表面张力均一、表观无瑕疵的要求,如无膜清洁处理装备与工艺,数十nm厚的无瑕疵真空磁控制溅射镀层实现是难以想象的。
(2)真空镀层厚度均匀性与表观质量瑕疵
任何产品金属镀层均存在厚度均匀性与表观质量瑕疵问题,真空磁控制溅射镀层工艺也不例外,其小面积静态真空磁控制溅射镀层质量或许表现结果较好,当大幅宽、连续化生产时会因系统真空度不稳定问题、非均匀溅射控制问题、非同步有效送收卷问题、冷却问题而变得复杂,任何一方出问题,均会产生料卷上(长度与宽度)非均匀溅射镀现象,也会出现漏镀、针孔、打皱现象,加之无厚度、CCD测定装置对连续镀层(对两面厚度同时测量尚存在技术难度)进行在线检测,连续无瑕疵导电层质量目标实现难度较大,生产效率也难以提升。
(3)真空镀层厚度量值及其设备产能分析
目前业界已经形成导电层厚度“共识”,单侧厚度大约在20~60nm范围,本人认为该“量值”值得商榷,应该研究透导电层增厚过程中“累积”效应(导电层增厚对抗剥离强度变化影响、镀层厚度不均匀变化加大影响)、导电层厚度对后续工序的合格率、成本、电耗的影响等关键问题,从中优化出不同产品铜厚所需最佳导电层铜厚数据;如无成本、累积效应的影响,理论上分析认为均匀的导电层越厚,越有利于第二步产品质量形成。据设备厂家介绍,真空磁控制溅射机可以以12m/min线速度生产双面20nm镀层的中间产品,单机理论产能可以达近800万m2/a,实际产能为300万m2/a(合6μm锂电池铜箔160.5吨),按单位时间溅射能力分析,其面积产能与导电层厚度成反比,考虑到成品率、负荷率、开工率的因素,实际产能可能更低;
(4)可溶性阳极对产品质量影响
从业界公布信息我们看到,加厚镀铜采用了碱性+酸性镀铜组合工艺,两种工艺均选用磷铜球(角)做铜原料--可溶性阳极,该工艺存在阴阳极间距随着磷铜球(角)溶解加大的固有缺陷,同时存在阳极溶解过程粉末化效应影响,如控制不当,将对镀层质量产生致命影响;
(5)阴阳极平行精度的影响分析
电解铜箔生箔机阴阳极为刚性约束,即便如此,其阴阳极间距同心度只能做到0.2mm,在此精度条件下,其面积质量极差也难以做±1%(相对误差),我们观察到“复合铜箔”加厚镀铜设备类似于电解铜箔的表面处理机,其阴阳极面皆为“非刚性约束”定位,阴阳极之间平行度、间距存在较大变化,其变化量是生箔机间距1~2个数量级,预计其镀层面积质量波动极差可能达±5%以上,甚至更高!
(6)导电辊镀铜及其影响
表面处理机阴极导电由导电辊承担,该导电方式就决定其导电辊“镀铜”不可避免性,即便做导电辊材质调整也无法彻底解决,根据电解铜箔表面处理经验,我们已知铜箔越薄,受导电辊“镀铜”影响越大,其生产效率降幅越大、成本升幅越大,如“复合铜箔”也采用该技术,那就是一个难以逾越“坎”!我们看到用PCB电镀使用的“导电夹”导电技术(主要用于静态电镀)可能应用到加厚“动态”镀铜设备中,能否达到预期还是个未知。
(7)单机产能受导电层厚度约束
目前电解铜箔表面处理机在处理12μm铜箔时质量可控的最大单槽电流为5000A,合单位铜箔截面积电流传输能力极限为300A/mm2,已是安全电流150倍以上,此时线速度在20m/m,箔面在电解液上停留时间小于小于3s(单侧,要注意该指标的意义!),铜箔表面剧烈发热,温度达60度以上,箔面水快速蒸发;比照该条件(以初始导电层厚度60μm计算),加厚镀铜机第一级电镀槽电流最高为12μm的1/100,即50A(双面),最后一级电镀槽最高电流为12μm的1/6,即1000A(双面),如加厚电镀整机按10级镀铜槽设置,其整机电镀电流小于5000A,每小时电镀铜沉积量大体为5.9kg,约可以形成330平方米2μm的铜镀层,合1300mm幅宽最大线速度只有4.3m/min(设备厂商已经报道给出7m/min生产速度),即便加到20槽,其最大线速度只有8.6m/min,预计实际运行电流还将小于理论计算值,实际产能更低;
(8)成品率问题
产品最终成品率是每步工序合格率的乘积,每一步工序过程合格率均对产品成品率产生“贡献”,表面上“复合铜箔”生产只有真空镀、加厚电镀、分切三道工序,如细分,应该还有基材处理、返切,如各级工序合格率为95%,其最终成品率为77%,如各级工序合格率为90%,其最终成品率为59%,从已知工艺设置、质量控制难度预测,按目前业界默认(实物质量)验收标准,预计产品成品率在底限区间,甚至更低!
(9)单位产能投资过高
目前看到了300万平方米“复合铜箔”产能需一台真空磁控制溅射机(报到报价1100万元)、两台加厚镀铜机(报到报价1200万元),三台设备的报价已达3500万元,这些还不包含真空系统、电解液储存系统、质量监测系统、公用工程系统(水、电、气)、厂房、酸雾净化、水处理系统、空调净化等投资,按其尺寸、功率估算,其未列入项的投资最少也得1500万元(实际上应该更高!),合计投资将达5000万元,这些投入最多可以生产300万平方米/年“复合铜箔”,相当于160.5吨6μm锂电池铜箔面积,而投资同样产能电解铜箔,最大800万元(按万吨锂电池铜箔产能固定资产投资最高5亿元计算),其单位产能投资是锂电池铜箔625%,目前锂电池铜箔单位产能年折旧、投资利息大体为合计为12%,合单位产能固定成本约6000元/吨(合0.32元/m2),参照计算,“复合铜箔”单位固定成本将达合2元/m2,这仅为理想值,如实际产出减小50%,其固定成本将达4元/m2。
(10)变动成本
同样产能(按面积计)“复合铜箔”设备投资是锂电池铜箔625%,且大多数为耗能设备,主要耗能设备有:主生产设备、净化恒温恒湿设备、环保(水供给、处理,废气处理,固体废弃物处理等)设备等,且主生产均以“高能量态”(溅射能损、高电流密度传输工艺用电能损)运行,其单位铜“沉积量”电耗大大高于电解铜箔(目前电解铜箔吨产品电耗低于8000kwh/t,6μm铜箔合0.43kwh/m2),初步计算,“复合铜箔”单位面积电耗是6μm电解铜箔1~2倍,预计单位面积“复合铜箔”(两面铜层厚度均为1μm)电耗在0.86~1.29kwh/m2区间,如电耗管理欠缺与达产率不足其电耗还将上升。
目前生产锂离子电池用电解铜箔全员劳动生产率在30吨/年水平(按6μm计算),按人均12万元/年(工资+“五险一金”)人工成本计算,吨均锂电池铜箔人力成本4000元,合6μm锂电池铜箔单位面积成本为0.21元/m2。
目前锂电池铜箔行业生箔岗位1人最少管理三台生箔机(DN2700设备),其面积产能相当于5×(一台真空+2台加厚镀铜机)“复合铜箔”生产设备的产出,而一台真空+2台加厚镀铜机最少需要6人值机,即该工序生产效率是电解铜箔1/30,考虑到其他岗位“拉平效应”,单位面积“复合铜箔”用工应该高于电解铜箔15倍,即单位面积“复合铜箔”人工成本大体为3.05元/m2。
锂电铜箔产生的废箔是循环利用,按成品率为80%,其仅要付出200kg/t额外溶铜质量成本,计算该成本为150元/吨产品,合6um锂电铜箔废箔质量成本仅为0.008元/m2。而“复合铜箔”就无法实现循环使用,其废箔只能当含铜废料出售处理,按照60%的成品率计算,18700平方米(合6μm锂电池铜箔1吨)将形成12470平方米报废,按2μm的铜厚计算,其金属量为222kg,如废品按铜价60%计算,18700平方米成品箔将产生40%×70元/kg×222kg=6216元质量成本,合单位面积铜报废质量成本为0.33元/m2,远高于锂电池铜箔的质量成本。
以上仅列出电耗、人工、质量三项主要变动成本项,分析得知,同样的产能(按面积计算),“复合铜箔”变动成本为4.67元/m2(高限),6μm电解铜箔为0.65元/m2,“复合铜箔”的变动成本是6μm电解铜箔的7.18倍;
经计算,立出项的“复合铜箔低限”固定成本+变动成本为6.67元/m2,高限成本为8.67元/m2,完全项合并计算,其变动成本还将更高。
2.2使用端面临技术难点
本人在2021年年会上发表了《 锂离子电池负极集流体应用质量实质研究》论文,该文章从宏观、微观角度分析了负极集流体在制造、使用、终端产品动态、静态充放电时的质量行为,较全面全面解读了锂离子电池用负极集流体应该具有的“质量性能”,比照该分析逻辑,以下对“复合铜箔”应用面临的“重点”技术、质量、经济难点进行分析。
(1)单面镀1μm铜层的“复合铜箔”可以安全使用到高倍率充放电动力电池中吗?
依据内阻模型,如用单面镀1μm铜层的“复合铜箔”替代6μm锂电池用电解铜箔使用,以同样电流进行充放电,其单位时间发热将增加三倍,电芯充放电电能内损增加三倍,随充放电倍率提高、电芯加大、电池组加大,热效应愈加明显,电芯、电池组热失控风险数倍增加!单面镀1μm铜层的“复合铜箔”能否用到较高充放电倍率动力电池做集流体取决于电池散热与管控技术进展,目前为止尚未看到突破!
(2)超薄铜层难以逾越负极压实质量关
为提升锂电池负极体积能量密度、负极材料与集流体的粘接强度,需对涂覆完成负极卷材进行压实处理,压实过程的巨大垂直压力在“凹凸不平”(微观层面)负极材料表面上形成“剪切力”,附着在“软基”PET膜上的1μm铜层,在“剪切力”作用下产生塌陷、断裂、与基膜分离“概率”大幅度增加,理论上负极材料不平整度越大、铜层越薄,其“剪切力”破坏越大,预计压实工序合格率(与用锂电池铜箔相比)将大幅度降低。
(3)极耳问题
主流电芯负极极耳由负极卷材“留白处”激光切出单极耳,单极耳组合形成阴极极耳,无须焊接;如“复合铜箔”也采用该方法,其“整极耳”由数个复合结构单极耳组成,复合结构使电流传输在厚度方向隔断,必须附加极耳“截面”导电工序,不知成本几何?
可能有人认为可以返回焊接极耳工艺,如如此,不但极耳要加倍(两面均要抽头),也将面临在1μm铜层焊接诸多质量难题(击穿、虚焊、脱焊等),总而言之,铜层减薄的“尺寸效应”与“复合结构”给极耳制造带来新的难题。
(4)基材耐老化、塑性形变性能对产品质量影响
PET、PP膜是目前行业主要选用基材,属线性高分子材料,为提升该类材料塑性与耐久性,一般会添加增塑剂与抗氧化剂,其长期在紫外线、酸碱盐、热环境时,增塑剂与抗氧化剂就会缓慢分解、消耗,随时间推移,轻者表现为物理性能衰减,重者表现为断裂、粉化;再有在外力作用下,会产生“塑性形变”,局部外力产生局部“塑性形变”,重度“塑性形变”将会发生铜层与基材“脱离”现象,这些都是业界要充分关注并要解决问题。
实际上“复合铜箔”应用还存在涂覆、倍率充放电过程面临高温、循环寿命、耐电解液与电解质化学腐蚀难题,鉴于篇幅限制,在此不做过多分析。仅依照以上重点分析,我们大体可以得出:a、单侧1μm铜厚复合铜箔替代6μm锂电池铜箔在锂电池应用时,难以实现6μm锂电池铜箔在锂电池内的“等效目标”;b、如使用单侧铜层加厚产品,如单侧铜层厚度2μm产品,或许锂电池产品性能指标离“等效目标”更近,但成本几乎会成倍上升;
2.3“复合铜箔”产品标准面临技术难题
(1)产品导电层厚度测量与标准指标量值的难题
锂电池铜箔实验室测量方法有三种,即称重法、螺旋测微器法(也称万分尺法)、截面显微测定法,仲裁方法为称重法;“复合铜箔”也可以采用类似方法测定,前两种测量方法测定数据是“三明治层”的复合总厚度,而非单侧铜的厚度,截面积显微测定法可以显示各层的厚度,但其检测费时、成本是前两种方法数十倍,如按目前行业对锂电池铜箔厚度检测频率,其检测成本将是数倍上升。
目前下游行业对锂电池铜箔厚度均匀性质量指标要求已达±2%(相对误差量值),如以此逻辑对“复合铜箔”两侧铜层厚度均匀性量值,其产品合格率将是“零”,预计放大数倍指标范围后,其均匀性指标合格率方可与锂电池铜箔行业表现水平相当,如如此,该指标量值失去“约束”、“满足下游需求”基本目的,下游行业难以接受!
(2)产品含铬量指标量值面临难题
目前锂电池行业接受铜箔中含铬量值≤100PPM,6μm及其以上厚度铜箔达标问题不大,厚度6μm以下的铜箔执行该指标已经有困难,已经出现较大百分比不合格现象!如对铜层总厚度仅为2μm“复合铜箔”采用同样量值(采用锂电池铜箔普片采用钝化工艺),并参照执行锂电池铜箔抗氧化与储存指标量值,其含铬指标均将不合格,这是我们必须面临难题,要么通过工艺进步使含铬量达标,要么放宽指标量值!
3.“复合铜箔”未来
基于锂离子电池用“复合铜箔”生产工艺、工序质量难点与质量成本、拟生产成本核算、使用机理、使用质量难点与成本、拟使用成本核算、产品质量标准编制与主要技术指标量值难点分析,我们认为以既有工艺(技术路线)生产、既有锂电池制造工艺使用的“复合铜箔”,在技术、质量、安全、成本乃至能量密度上,与锂电池用电解铜箔不具备技术、经济竞争的可比性。
对于极小规模实验室出品的锂离子电池用“复合铜箔”,有可能在下游部分客户(忽略成本、质量焦虑的情况下)中得到研发试验应用,实验产品能否以批量交付到终端客户不得而知。我本人没有公开层面能获取的批量应用的相关案例,在此保持谨慎和关注的态度。
在下游电芯客户及终端应用客户对上端供应链材料逐年降本的基本采购宗旨下,锂电池用“复合铜箔”就现状的技术而言,且不说能否大规模生产,其目前高于电解锂电铜箔6倍余的生产成本和近乎10倍余的投资成本,短期内代替电解锂电池铜箔的可能性极小。下游行业应用信息的缺失、产品质量标准的不可确定性应证了我们今天分析的结论。
鉴于锂电池用“复合铜箔”概念提出并非源于本行业,迄今为止,行业协会未组织行业人士分析、研究“复合铜箔”替代电解铜箔在锂离子电池中应用的技术、经济可行性,也没意识到“复合铜箔”过渡宣介对电解铜箔行业可持续性发展的影响,基于成员义务与本人“职业生涯”技术积累,花数天撰写此文,是基于技术+生产管理研究与探讨,无任何商业目的,仅为电解铜箔产业链健康发展服务。
新能源汽车的快速发展带动了动力电池的高速增长。动力电池生产流程一般可以分为前段、中段和后段三个部分。其中,前段工序包括配料、搅拌、涂布、辊压、分切等,中段工序包括卷绕/叠片、封装、烘干、注液、封口、清洗等,后段主要为化成、分容、PACK等。材料方面主要有正负极材料,隔膜,电解液,集流体,电池包相关的结构胶,缓存,阻燃,隔热,外壳结构材料等材料。 为了更好促进行业人士交流,艾邦搭建有锂电池产业链上下游交流平台,覆盖全产业链,从主机厂,到电池包厂商,正负极材料,隔膜,铝塑膜等企业以及各个工艺过程中的设备厂商,欢迎申请加入。
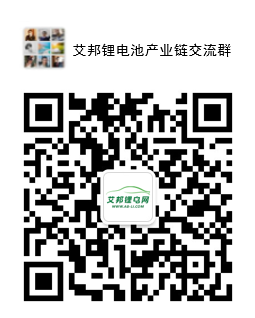
长按识别二维码关注公众号,点击下方菜单栏左侧“微信群”,申请加入群聊