硅基负极复合材料有三种技术路径:硅氧负极、硅碳负极和硅基合金负极。
硅碳负极是指纳米硅与石墨材料复合,硅氧负极则采用氧化亚硅与石墨材料复合,硅基合金负极是指将硅粉与其他金属复合。
硅碳负极材料的首效较低,且循环性能不佳,膨胀率在300%以上目前主要应用于消费电池领域,工艺相对比较成熟,贝特瑞、国轩高科、日立化成等均有布局。
硅氧负极材料的首效较低,循环性能一般,体积膨胀率相较硅碳负极更低,但生产成本高,璞泰来、贝特瑞、特斯拉等有布局。
硅基合金负极的首次效率与循环性能均表现较差,工艺复杂、生产成本高,但硅基合金负极的能量密度高,主要应用于动力电池领域。
鉴于硅碳负极工艺较为成熟、硅氧负极整体性能优越,以及硅基合金负极的成本高,目前硅基材料以硅碳负极与硅氧负极为主。
首次效率 |
循环性能 |
膨胀率 |
主要厂家 |
优点 |
缺点 |
|
硅碳负极 |
88-89% |
500-600圈 |
>300% |
贝特瑞、国轩高科、日立化成、LG化学 |
材料的容量高,且工艺比较成熟 |
技术壁垒较高,难以大规模批量生产,循环性能较差,且存在体积膨胀问题 |
硅氧负极 |
<90% |
700-800圈 |
>100% |
贝特瑞、杉杉股份、特斯拉、信越 |
材料的容量高,循环性能与倍率性能相对一般,体积膨胀率较低 |
首效较低,生产成本较高 |
硅基合金负极 |
80-85% |
200-300圈 |
<100% |
日立化成 |
能量密度高 |
循环性能差,工艺复杂,生产成本高,首效低 |
资料来源:电子发烧友
制备工艺
硅基负极材料的制备工艺主要有机械球磨法、化学气相沉积法、溶胶-凝胶法、高温热解法,静电纺丝法。由于硅碳负极和硅氧负极分别采用纳米硅和氧化亚硅与石墨混合,故两种负极材料的前端程序不同,而后端工序(前驱体的表面处理、筛分、除磁包装、成品)基本相同。
方法 |
优点 |
缺点 |
化学气相沉积 |
循环稳定性好,首次充放电效率高,设备简单,适合工业化生产 |
总比容量较低,设备复杂,成本较高 需要与其他方法组合使用 |
机器球磨法 |
明显降低反应活化能,提高材料电学、热学性能 |
需要根据硅与石墨的亲和性选择合适的研磨条件,产生较多微晶颗粒,易引发副反应 |
静电纺丝法 |
低成本,工艺简单 |
能耗较高 |
溶胶-凝胶法 |
分散性好,较高的可逆比容量,循环性能好 |
产品易发生团聚 |
高温热解法 |
工艺简单,易产业化,能够较好的缓冲充放电过程中的体积变化,产品一致性较好 |
硅的分散性较差,包覆一致性不高,易发生团聚 |
性能优化路径
硅碳负极克容量更高,首次效率高,但体积膨胀较大导致循环性能相对较差。硅氧负极体积膨胀大大减小,故循环性能更好,但首次效率较低。
材料设计和电池体系优化是提升硅基负极材料性能的主要方式:
1.材料设计,通过硅的纳米化、对硅进行碳包覆、加入氧化亚硅等方式,减小体积变化带来的负面影响。
2.电池体系改进,目前主要是通过电解液添加剂、负极材料粘接剂、导电剂的优化来减少硅基负极的膨胀影响。
3.电极结构改进,省去粘接剂或集流体,直接将活性材料复合在导电网络中制得极片,该技术路线处于研发阶段。
方法 |
技术原理 |
纳米化 |
纳米材料往往具有更小的尺寸以及更高的比表面积。同时,纳米材料表面的原子也具有更高的平均结合能。因此,它们可以在体积膨胀过程中更好地释放应力,有效地避免自身结构的坍塌,从而保持电极的壳容量,提升电池的循环性能。 |
碳包覆 |
一方面可以将硅表面很好地保护起来,并充当硅体积膨胀的缓冲层,避免硅在充放电体积形变过程中裸露的新鲜硅表面与电解液直接接触反复生成 SEI 膜;另一方面可以增加颗粒的导电性,促进锂离子和电子在硅颗粒和电解液之间的传输,较少电极的电荷转移阻抗。碳包覆方案有核壳结构、多孔结构和空心核壳型等。 |
氧化亚硅材料 |
将硅、二氧化硅相混合成一个新的结构。在该结构中存在硅、二氧化硅和一些硅的亚氧化态。氧化亚硅材料由于其中的硅为无定型态或者晶粒减小的晶体硅(一般小于 10nm),而且在首次嵌锂时会形成硅酸锂和氧化锂的缓冲层,一般会表现出更好的循环性。但是同时也由于二氧化硅和硅的一些亚氧化态会在首次嵌锂时不可逆地消耗一些活性锂生成硅酸锂和氧化锂,氧化亚硅材料一般会表现出较低的首周效率。 |
硅/金属合金 |
某些金属(如 Ge、Sn、Fe 等)与硅合金化使用可以稳定结构,提升电机循环寿命和倍率性能。硅/金属合金生产工艺复杂,尚不能大规模生产。 |
预锂化 |
预锂化能够提前在材料内引入活性锂,避免了全电池中有限锂源的过度消耗,可以大幅提高材料的循环性能。预锂化技术主要有负极补锂、正极补锂。 |
电解液的改进 |
电解液直接影响硅负极的 SEI 成膜过程,一个致密均匀且具有离子电导的 SEI 膜直接影响到硅负极的循环稳定性。一般 EC、DEC、DMC 成分变化不大,研究发现 FEC、VC、LiBOB 等添加剂对硅基负极有效果。 |
粘结剂的改进 |
合适的粘接剂有利于减少硅负极的体积膨胀和在硅表面形成连续的 SEI 膜。选择合适的粘接剂时,首先考虑表面基团,羟基和羧基等极性官能团有利于粘附在硅颗粒表面,如 CMC-SBR 体系;其次,还要考虑粘结剂的碳链结构,碳链较长且没有支链有利于硅负极膨胀收缩过程中的滑动,而不是直接与硅颗粒脱离。目前,硅负极容量在 500mAh/g 以下,一般选择 CMC-SBR 体系;硅负极容量 550mAh/g 以上,选用新的粘结剂。常用的高容量粘结剂有聚丙烯酸和聚丙烯酸锂。 |
导电剂的改进 |
硅基负极的导电性能比天然石墨和人造石墨等石墨类负极材料要差,因此需要添加高性能导电剂来提升其导电性能。碳纳米管导电剂是目前的主要方向之一。 |
新型硅基电极结构 |
活性材料直接复合在导电网络中制作极片,省去粘接剂或集流体。目前实验室阶段研发出利用静电纺丝制备出了嵌有硅材料的复合材料直接用作电极,Si/C 复合纤维织成的片状材料容量达 952mAh/g。此外,自支撑无需粘接剂和集流体的电机也处于研发中。 |
资料来源:电子发烧友、头豹研究院,中信证券,新时代证券等
锂电产业通公众号里的内容包括锂电池产业链交流、资讯、人脉圈。从正负极材料生产到涂布,隔膜、电解液、封装材料到检测组装等这些环节涉及的材料、辅材、添加剂、耗材,以及相关设备,相关企业介绍。
原文始发于微信公众号(锂电产业通):硅基负极复合材料的制备工艺及性能优化路径
新能源汽车的快速发展带动了动力电池的高速增长。动力电池生产流程一般可以分为前段、中段和后段三个部分。其中,前段工序包括配料、搅拌、涂布、辊压、分切等,中段工序包括卷绕/叠片、封装、烘干、注液、封口、清洗等,后段主要为化成、分容、PACK等。材料方面主要有正负极材料,隔膜,电解液,集流体,电池包相关的结构胶,缓存,阻燃,隔热,外壳结构材料等材料。 为了更好促进行业人士交流,艾邦搭建有锂电池产业链上下游交流平台,覆盖全产业链,从主机厂,到电池包厂商,正负极材料,隔膜,铝塑膜等企业以及各个工艺过程中的设备厂商,欢迎申请加入。
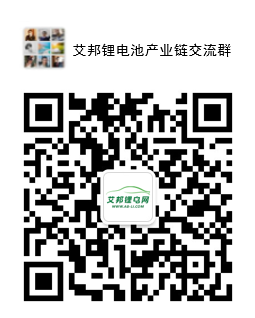
长按识别二维码关注公众号,点击下方菜单栏左侧“微信群”,申请加入群聊