这几年,电池结构演进成为电池企业技术发展的主流方向。以宁德时代、比亚迪和特斯拉为代表的企业,都在不断改进电芯形状和电池结构。
目前来看主要分为三代产品,CTP(Cell to Pack)、CTB(Cell to Body)和CTC(Cell to Chassis或Cell to Car),逐级发展集成度越来越高。
▎CTP技术 宁德时代 & 比亚迪
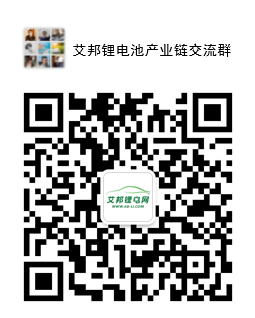
▎特斯拉 CTC方案和一体化压铸技术
▎零跑汽车“CTC电池底盘一体化”技术
零跑汽车的自研化成果,利用车身设计实现电池密封,CTC技术借用底盘基本结构,利用车身纵梁、横梁形成完整的密封结构,解决气密难题,相对于传统汽车这是一大创新。
CTC技术为电池布置空间增加14.5%,车身垂直空间增加10mm,更高的电池空间利用率,以及冬季保温性能更加,车辆综合续航增加10%。
而车身轻量化系数相比传统方案提升20%,车身扭转刚度提升25%;车端BMS实时在线检测,云端电池大数据管理并通过AI深度学习,实现车端云端全时主动守护。
此外,零盘的CTC技术还有高适、强扩展特性,与整车匹配度高,可快速柔性化量产,未来能够适配各级别车型;同时,智能化、集成化热管理系统,未来能够兼容800V高压平台,提升充电体验。
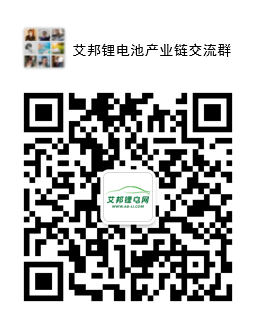
▎比亚迪CTB电池车身一体化技术
5月20日,比亚迪发布了CTB电池车身一体化技术,同时宣布首款搭载了CTB技术的e平台3.0车型——海豹开启预售,预售价格为21.28-28.98万元。
比亚迪CTB电池车身一体化技术简化了车身结构和生产工艺。得益于CTB技术的优势,海豹在安全、操控、高效和美学方面都实现了新的突破,性能表现更优。
CTB电池车身一体化技术,将电池上盖与车身地板进一步合二为一,从原来电池包“三明治”结构,进化成整车的“三明治”结构。动力电池系统既是能量体,也是结构件。这种融合简化了车身结构和生产工艺,是对传统车身设计的一次颠覆性变革。
CTB刀片电池包的结构灵感,来源于蜂窝铝结构。刀片电池本身非常安全,相邻电芯可以紧密排列在一起。一排排的刀片电芯组成的结构就如蜂窝芯,通过上盖板和底板组成类蜂窝结构。这让CTB刀片电池包的结构强度得到突破,能够顺利通过50吨重卡碾压的极端测试。
同时,CTB技术实现了车身与电池系统的高度融合,整车扭转刚度提升一倍。搭载CTB技术的纯电动车型,车身扭转刚度可以轻松超过40000N·m/°,媲美百万级的豪华车,让燃油车的上限成为了电动车的下限。
CTB技术实现了整车强度和刚度的提升,进而实现了安全性能的提升,可以满足“超五星”的安全标准。搭载CTB技术的e平台3.0车型,正碰结构安全提升50%,侧碰结构安全提升45%。CTB技术能够打造“撞不断的电动汽车”。
▎CTP、CTB和CTC技术对比
CTP只是电池包内部的整合,取消模组或者变成更大模组的概念,简化结构件,电池的体积能量密度和生产销量得到明显提升,生产成本有所下降。
零跑汽车CTC相对比亚迪的CTB要简单一些,前者只是直接取消了电池包的上盖与整车集成,车身和地板不变。零跑的方案并没有做电芯直接集成,而是采用了模组集成的方式,集成度也不如比亚迪的CTB。
特斯拉是电池和车身的完全一体化:车身变动最大,取消原有座舱底板,取代以电池上盖,座椅直接安装在电池上盖上。
技术名称 | 特点 | 整合方式 | 优点 | 缺点 |
CTP | 电芯-电池包 | 大模组或无模组,电池包结构内部简化。 | 电池组体积利用率提升15%-20%, 零件数量减了40%,简化模组工艺,让生产效率提升50% | 电芯更换难度较高,电池和车身没有一体化,集成度仍有提升空间。 |
比亚迪CTB | 电芯-车身 | 电池上盖一部分是座舱底板,还有部分电池包结构。 | 电池车身一体化, 整车扭转刚度提升 一倍,突破40000N·m/°。搭载CTB技术的e平台3.0车型,正碰车内结构安全提升 50%,侧碰车内结 构安全提升45%。 较CTP方案,CTB使 振动速率和振幅降 低90%,路噪降低 1.5dB。 | 仍然保留电池包结构,集成度仍有提升空。 |
零跑CTC | 电芯-模组-底盘 | 零跑是将电池包的上盖板去 掉,保留模组 结构。 | 垂直空间增加 10mm,比传统方案 电池布置(电池包 方案)空间增加 14.5%;续航提升 10%。让零部件数 量减少20%,结构 件成本减低15%, 整车刚度提高 25%,简化了总装 工艺,高度集成化 和模块化。 | 保留模组,没做到最大程度上的整合。 |
特斯拉 CTC | 电芯或模组-底盘 | 前车身+底盘电池包+后车身组合成车身。取消原有座舱底板,取代以电池上盖,座椅直接安装在电池上盖上。 | 结合一体化压铸, 为车辆降低10%重 量,增加14%续航 里程,减少370个 零件,单位成本下 降7%,单位投资下 降8% | 电池不能更换,维修成本高。 |
数据来源:《电动汽车观察家》整理
当然,缺点也很明显,随着集成度越来越高,电池的维修难度越来越大,到了CTC阶段,电池是不能更换的。这对电芯的一致性、可靠性提出了非常高的要求。
来源:
比亚迪CTB技术全球首发,首搭车型海豹;华声在线,艳红,2022年5月,
比亚迪CTB技术,电池结构化天花板;新能源车咨询,网易,2022年5月,
比亚迪车身电池一体化一小步,车辆性能一大步;第一电动,电动汽车,
国海证券:特斯拉生产制造革命:4680 CTC,
比亚迪,零跑科技,粉体网等
原文始发于微信公众号(锂电产业通):CTP、CTB和CTC电池技术对比!
新能源汽车的快速发展带动了动力电池的高速增长。动力电池生产流程一般可以分为前段、中段和后段三个部分。其中,前段工序包括配料、搅拌、涂布、辊压、分切等,中段工序包括卷绕/叠片、封装、烘干、注液、封口、清洗等,后段主要为化成、分容、PACK等。材料方面主要有正负极材料,隔膜,电解液,集流体,电池包相关的结构胶,缓存,阻燃,隔热,外壳结构材料等材料。 为了更好促进行业人士交流,艾邦搭建有锂电池产业链上下游交流平台,覆盖全产业链,从主机厂,到电池包厂商,正负极材料,隔膜,铝塑膜等企业以及各个工艺过程中的设备厂商,欢迎申请加入。
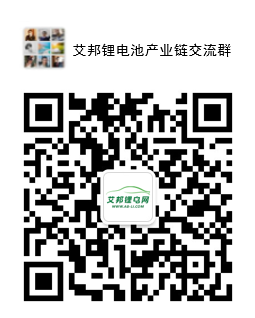
长按识别二维码关注公众号,点击下方菜单栏左侧“微信群”,申请加入群聊