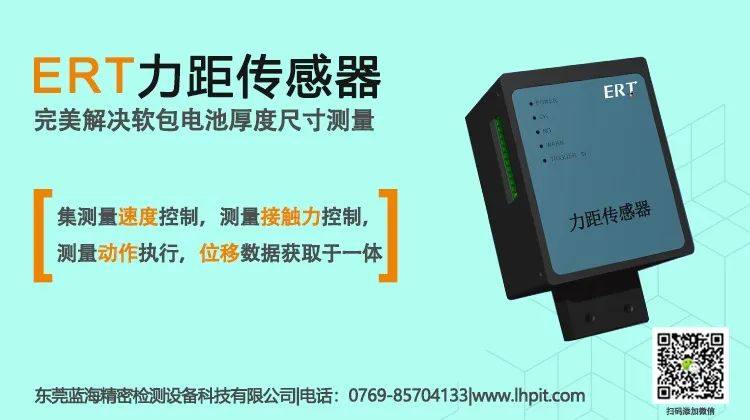
近期宁德时代时代推出了第三代CTP动力电池——麒麟电池,据悉,由于CTP3.0 电池中的水冷板具有缓冲作用,所以比其它动力电池寿命更长,并且比能量、电池空间利用率都有大幅提升,在相同的化学体系、同等电池包尺寸条件下,磷酸铁锂系统能量密度 160wh/kg,三元高镍可达 250wh/kg,较特斯拉的4680电池多装30%的电量。
而在宁德时代的麒麟电池推出之前,动力电池的聚光灯一直照在新能源汽车巨头特斯拉推出的4680电池上。 据悉,4680 电池相比 2170 电池,虽然是体积增加了 448%,但是与全极耳、高硅负极、与 CTC 结合等更多革命性的技术相结合,最终实现了续航增加 54%,成本下降 56%,单位产能设备投资额下降 69% 优良成绩。
从电池结构来看,宁德时代的麒麟电池走的是CTP路线,而特斯拉的4680电池则走的是CTC路线。就目前来看,CTP 结构已经成为主流,毕竟宁德时代在最新的市场调查报告中显示,其依旧以33.9%的全球市场份额卫冕动力电池冠军。但是CTC无论是在外形、材质、组合形式上的一体化、集成化程度都更高,也是未来电池技术方案发展的重要方向,那么未来动力电池结构之争究竟是 CTP一统江湖还是CTC 技高一筹呢?
动力电池最常见的结构并非CTP与CTC,而是更为传统的MTP结构。传统电池包MTP是电芯、模组成组电池包的形式,多个电芯组成一个模组,多个模组加上BMS、配重模块等零部件则组合成电池包。在MTP结构下,电芯被外部结构件充分地保护所以结构强度好,成组难度小。但是,传统的MTP结构对于电池包的空间利用率极低,仅为40%,其中电芯对模组的空间利用率也只有80%,模组对电池包的空间利用率为50%,所以随着市场对新能源汽车需求的不断提升(续航),MTP结构已无法满足智能汽车的发展需求。
2019年9月,宁德时代全球首款CTP电池包量产下线,搭载于北汽EU5。比亚迪紧随其后,于 2020年3月发布其创新技术刀片电池。此后国内外整车厂、电池厂在CTP技术上各显神通,推出了不同的代表作品。
CTP相较于MTP省去了中间模组环节,CTP技术是将电芯直接成组为Pack,省去组装为传统模组这一步骤,先将电芯集成到电池包内,再安装到车身上,本质是为了提高能量密度和降本。
目前主要有两种思路,一是将Pack看成是一个完整大模组替代内部多个小模组的结构,逐步减少端侧板等结构件的方式,以宁德时代为代表;二是设计时即考虑采用无模组方案,以电池本身作为强度的参与件去设计,以比亚迪刀片电池为代表。
而CTC本质上就是底盘平台化的思路,理论上电量能在现有底盘技术上提升5%,持续提高汽车电气化程度。CTC电池集成方案主要有两种,第一种是电池包底盘集成,是直接将电池包集成到底盘框架中,从而代替地板,或者直接使用乘员舱地板作为电池的上盖,实现车身地板和底盘一体化设计;第二种是电池单体底盘集成,是将电池单体的壳体焊接或者胶粘,连接到底盘结构上,改变了电池的制造形式。前者可靠性高,后者集成优势明显但技术难度大且无法换电。
其实CTP与CTC是各有优势也各有短板,CTP 方案直接将单体电芯组成一个或几个阵列(模组),安装到电池包中,大幅减少了模组的数量,免去了先形成模组再安装成电池包的过程和其中的成本,形成电池包后可安装至新能源汽车上。
使用 CTP 技术后,提高了电池包的空间利用率,提升了体积能量密度,减少了不必要的模组零部件,但对技术能力的要求提高,安全性能不如模组叠加的组合方式。
而CTC方案的优势则是更高度的一体化与集成化所带来的容量提升与空间利用率的提升,当然也有不容忽视的短板——安全与成本。
根据未来新能车的市场空间和CTP/CTC 的渗透速度,预计CTP/CTC 的市场空间及其变化。我们预计2024年,CTP和CTC渗透率能达到 90%,预计 2022至2027年CTP和CTC装机量持续提升,合计将于2025年超越千万辆,而无论是CTP方案还是CTC方案,一体化、集成化都是其发展的方向。
电池包技术从 MTP 发展到 CTC,零件的外形、材质、组合形式等都伴随电池集成技术的进步发生了改变,整体的方向是一体化、集成化。独立的零件变少,几个零件统一集成到一个零件中去,形成尺寸更大、功能多元的大零件。零件方面的变化带来供应商的改变,市场格局也将被重塑。
随着未来 CTP 或者 CTC 的普及,系统的集成度越来越高,将会加大胶的用量,CTP 预计用量水平翻倍。pack 里面常见的胶分三种:导热胶,结构胶,密封胶。
用量最大的是结构胶,凝固之后能够提供一定强度,作为结构支撑;导热胶用来传导电芯或模组之间的发热,与水冷系统接触;密封胶水在接口密封,价值量含量最低。涂胶的难点是电池制造环境,核心是涂胶路径和工艺参数的设计。一般导热胶优先涂在底部,结构胶涂抹根据设计来定。
伴随电池包结构的变化,水冷系统也随之发生变化,一是水冷板从之前的单一结构变成集成化结构,比如沃尔沃 CTC 技术路线中,冷却技术上采用的是底部一体式水冷板技术。二是电池之间增加云母板或隔热垫,在整个热管理系统中发挥其绝缘性强、耐高温的作用,比如特斯拉的 4680+CTC 技术中,箱体底部就运用了云母板方案。
目前,特斯拉采用 4680+CTC,以电池上盖代替座舱地板,壳体焊接横梁增加强度;BYD 将电池车身一体化技术称为 CTB,将电池上盖与车身地板进一步合二为一,电池包托盘构成蜂窝状结构,与刀片电池结合加强侧向吸能和抗冲击力,由此可见一体化、集成化是未来动力电池的发展趋势。
来源:动力电池结构之争:CTP VS CTC;科技智谷、电车测试,2022年7月
原文始发于微信公众号(锂电产业通):动力电池结构之争:CTP VS CTC
新能源汽车的快速发展带动了动力电池的高速增长。动力电池生产流程一般可以分为前段、中段和后段三个部分。其中,前段工序包括配料、搅拌、涂布、辊压、分切等,中段工序包括卷绕/叠片、封装、烘干、注液、封口、清洗等,后段主要为化成、分容、PACK等。材料方面主要有正负极材料,隔膜,电解液,集流体,电池包相关的结构胶,缓存,阻燃,隔热,外壳结构材料等材料。
为了更好促进行业人士交流,艾邦搭建有锂电池产业链上下游交流平台,覆盖全产业链,从主机厂,到电池包厂商,正负极材料,隔膜,铝塑膜等企业以及各个工艺过程中的设备厂商,欢迎申请加入。
长按识别二维码关注公众号,点击下方菜单栏左侧“微信群”,申请加入群聊