01
研究背景
随着化石燃料的逐渐枯竭和环境污染问题的不断加剧,纯电动汽车因其绿色环保的特性,受到各国的高度重视。近年来,我国也从政策和补贴方面大力推动纯电动汽车的发展。电池包作为纯电动汽车的核心部件,其质量(包括电池组)一般约占整车质量的30%~40%。对纯电动汽车而言,整车质量下降10%,可减少5.5%的电能损耗,同时增加5.5%的续驶里程。
电池包是由电池模组及其外壳组成,它的主要功能是固定、保护和承载电池模组,其壳体约占电池包总质量的20%~30%。由于电芯能量密度的提升缓慢,所以减少电池包箱体质量是提升续驶里程的重要方法之一。
汽车在实际行驶中,会经受颠簸、急转弯、紧急制动、路面激励等复杂工况的影响,以此受到的外部冲击和振动会导致电池包箱体变形过大和应力集中,进而挤压电池模组引起内部短路、起火和爆炸。
因此,电池包结构和性能的安全性对整车的安全性能有重要影响。在此基础上的轻量化研究,对纯电动汽车未来的发展具有重要意义。
此外,实现轻量化的电动汽车,其续驶里程更长,更受市场欢迎。因此,轻量化的电池包外壳必须具有较高的强度和抗振动性。 02 国内现状
目前,国内在电池包的结构设计和轻量化方面做了大量研究。华南理工大学陈元设计了一款轻量化电池包,分析了电池包在不同工况下的静态应力、应变分布,同时开展在低阶模态约束下,电池包质量与静态载荷变形量的双目标优化,在不降低性能的前提下实现电池包质量减轻29.1%,一阶模态频率由23.60Hz提升至27.60Hz。
湖南大学王品健对某款纯电动汽车电池包进行了动静态特性分析,得到电池包的一阶模态频率24.06Hz,接近路面激振频率,再采用材料替换、尺寸和拓扑优化等方式对电池包结构进行优化设计,优化后电池包的动静态性能得到明显改善,实现质量减轻6.3%,频率提高至49.37Hz。
侯文彬等以某款电动汽车电池箱为优化对象,通过有限元模拟分析了电池箱在不同工况下的强度和刚度,采用等代设计法进行多工况的整体优化,优化后电池箱质量下降29.9%,强度和刚度得到大幅提升。
马其华等基于碳纤维复合材料成型和力学替代性要求,设计了一体化车架-电池托盘结构,并对结构进行不同工况下的静力学分析,又在此基础上用OptiStruct软件对结构进行铺层优化,优化后的结构满足各工况载荷要求,总质量减轻30%。
湖南大学杨书建基于某企业的一款电池箱结构,采用有限元法对结构进行了静态、模态和定频振动特性分析,发现了电池箱强度和刚度的薄弱位置,采用优化设计法对结构进行改进,实现强度和刚度提升的同时,箱体质量减轻7.2%。
东南大学刘元强基于目标车型设计了一款动力电池包,对结构进行了静力学、自由模态、谐响应以及定频振动分析,得到电池包的一阶固有频率(58.13Hz)高于路面激励频率,最大应力均小于结构屈服强度,满足极限工况下的使用要求。李垚坤等以某电动汽车电池包为研究对象,采用Abaqus软件对结构进行了颠簸紧急制动工况下的静力学特性以及随机振动分析,基于响应结果对结构进行改进,实现结构强度和刚度提升的同时,电池箱质量减轻48.7%。
合肥工业大学程文文采用熔模铸造工艺设计铸造铝合金一体化电池包,分析了电池包动静态特性,发现最大应力远小于屈服强度,存在强度过剩。进行多目标尺寸优化设计,电池包在满足动静态特性以及疲劳寿命要求的前提下质量减轻15.05%。 03 轻量化方法 电池包轻量化是在保障其各项服役性能不降低的前提下,合理选用材料和优化结构性能使电池包质量减轻的技术过程。
本文通过总结不同品型电池包在结构设计、箱体材料选用、静态特性和动态特性4个方面的性能参数,从材料的角度出发,比较满足4个方面要求的轻量化电池包用材料的服役性能,评估不同材料的轻量化效果,为选用合适的材料用于电池包的轻量化结构设计提供参考。
a. 电池包结构设计分类 在电池箱质量减轻的情况下,电动汽车可多配备同等质量的电池,相应地增加续驶里程。下图从结构设计总结同品型电池包的质量与体积的关系比较不同品型电池包结构性能。 由图a可知,钢铁材料电池包的质量范围为11.38~205.90kg,对应体积范围为0.05~0.71m3;铝合金电池包质量范围为3.45~75.90kg,对应积范围为0.04~0.56m3。可见,在同等质量下,铝合金电池包的体积更大,有利于空间内电池模组的优化排布;同等体积下,铝合金电池包的质量更轻,可以多配置同等质量的电池,延长续驶里程。
b. 材料设计分类 目前,高强度钢、铝合金、复合材料在电池包箱体的轻量化中扮演重要角色。高强度钢具有屈服强度和拉伸强度高、抗变形、减震吸能强、焊接工艺成熟等优点,但同时也存在自重过大、耐腐蚀性差等缺点。 铝合金是一种广泛应用在汽车领域的轻质材料,其密度只有钢的1/3,相比于传统钢材具有质量轻、可塑性好、比强度高、耐腐蚀、导热和散热性好、易回收利用等优点。导热系数,铝为237W/(m·K),铁为80W/(m·K)。电池箱盛装电池在消耗过程中会散发大量热量,选用铝合金作为电池箱材料具有明显优势。 复合材料具有密度低、比模量高、抗腐蚀、耐磨损、成型性和冲击性能好等优点,且质量只有钢的1/4,但也存在成本高、回收利用率低、散热性差等缺点,在汽车中的应用仅限于性能车领域。目前,应用铝合金降低车身质量已成为纯电动汽车发展趋势。图(b)为不同类别材料与比强度的关系。 由图可知,电池包箱体用铝合金材料的比强度均显著高于箱体用钢铁材料。在铝合金材料中,Al-S-6000的比强度最低,为52.22MPa/(g·cm-3),与钢铁材料中比强度最高的B410LA的数值60.51MPa/(g·cm-3)接近,可见铝合金材料的轻量化优势显著。
但是其应用量却没有钢铁材料广泛,一个重要的原因是成本效益,铝合金的成本是钢铁材料的2倍左右,对于追求长续驶里程的电动汽车,采用铝合金电池包是使汽车轻量化以提升续驶里程的重要途径,但无疑会造成整车成本的增加,所以对于中等续驶里程的汽车通常选用钢铁材料作为箱体材料。因此,开展高性能低成本铝合金研制是未来发展方向。
c. 静态载荷分布分析 对电池箱进行静力学分析是为了计算电池箱结构的承载能力,在不同工况下所受应力是否超过材料的屈服极限等。
通过查阅相关文献可知,紧急制动、急转弯和颠簸工况对电池箱的冲击作用较大,电动汽车在紧急制动、急转弯或经过颠簸路面时,电池模组会因惯性对电池箱产生纵向、侧向和地面冲击载荷,其作用力远超正常工况,特别是冲击载荷,远大于静态载荷。
因此,在颠簸路面上行驶属于极限工况。本文总结了两种工况下最大应力与安全系数、应力集中位置及发生概率的关系。
颠簸路面急转弯工况:该工况下,颠簸作用的最大应力作用于电池箱底面,急转弯作用的最大应力作用于电池箱的大侧面。图3a为颠簸急转弯工况下的最大应力和安全系数的关系。
由图可知,铝合金电池包的最大应力主要集中在22.34~140.80MPa之间,小于钢铁材料的应力范围41.62~195.40MPa;铝合金电池包的安全系数范围1.58~12.76,大于钢铁材料的安全系数范围1.09~7.33。
组合工况下的安全系数均>1,表明箱体所受应力均低于材料的屈服强度,电池箱箱体没有发生屈服失效,强度和安全性良好。
由此可知,在该工况下,铝合金电池包的应力集中小且安全系数高,即服役性能更好。因此,在满足结构静态特性的前提下,箱体选用铝合金材料,可同时实现有效减轻质量和提升安全性能。 图3b为颠簸急转弯工况下应力集中位置与发生概率关系。由图可知,应力主要集中在下箱体。该工况下的最大应力按概率易发生在下箱体吊耳、托架螺栓孔、下箱体底面和下箱体侧围。
这是由于颠簸急转弯时,箱体里面的电池由于惯性作用向急转弯和颠簸最大加速度的合成方向运动,两者加速度的合成方向指向电池包转弯的大侧面,所以电池箱底面偏向大侧面受到的力比较大,对应靠近大侧面的托架、吊耳受到的力也比较大。
由于吊耳与托架起约束电池包位移的作用,此处的螺栓孔应力集中比较明显。电池箱直接承载电池的重量,箱体与电池模组支架之间属于线接触,所以在箱体底面存在应力集中。
颠簸紧急制动工况:颠簸紧急制动工况下的静力学分析,如图4所示,在该工况下,颠簸时的最大应力作用于电池箱底面,紧急制动时的最大应力作用于电池箱的小侧面。
图4a为颠簸紧急制动工况下最大应力与安全系数的关系。由图可知,铝合金电池包的最大应力范围为22.1~142.6MPa,小于钢铁材料的应力范围37.11~185.04MPa。
铝合金电池包的安全系数范围为1.71~12.90,高于钢铁材料的安全系数范围1.07~8.22,且同等应力条件下的安全系数是钢铁材料的1.2倍左右。同样,在该工况下,铝合金电池包的服役性能更好。 图4b为该工况下应力集中位置与发生概率关系。同样,应力主要集中在下箱体。最大应力按概率易发生在下箱体吊耳、托架螺纹孔处、下箱体底面以及承受紧急制动产生的冲击力的小侧面。
这是由于紧急制动时,箱体里面的电池因为惯性作用继续向前运动而对前面的小侧面产生了一定的冲击力,颠簸情况下电池上下振动产生的力作用在电池箱底面,并通过模组支架再传递到托架、吊耳上,应力出现在约束箱体位移的吊耳和托架的螺栓孔处。
d. 动态载荷分布 汽车零部件设计时通常都会将一阶模态频率作为一项基本指标,当汽车自身零部件与行驶时路面的激振频率处于同一区间时,将会极大地降低整车的安全舒适度,同时也会发出共振噪声。
对电池箱的模态分析可以得到箱体的一阶固有频率和振型,从振型上可以找出箱体结构刚度不足的地方进行优化设计。
查文献可知,路面引起车身的振动频率通常在1.32~27.78Hz区间,所以在设计电池箱体时,其一阶模态频率需要高于路面激振频率,以便有效地减小该频率区间对箱体的激振。
由图5a可知,随着电池包质量的增加,一阶模态频率存在下降的趋势,所以电池包过重会增加与路面激励共振的风险。铝合金电池包的一阶模态频率范围28.22~102.34Hz,高于钢铁材料的一阶模态频率范围为30.22~58.13Hz。
因此,使用轻量化的铝合金材料在减轻箱体质量的同时,可提高低阶模态频率,从而有效避免外界激励,减少电池包的振动损耗。由图5b可知,振动发生在上箱体的概率是62%,下箱体的概率是26%,箱体侧壁的概率是8%。顶盖部分发生振动弯曲变形的概率较大,容易引发共振,降低电池箱的使用性能和疲劳寿命。
由于上箱体不承重,在满足轻量化的同时,还要提高其一阶模态频率,因此铝合金是合适的材料。其次是箱体底面及侧壁,出于结构安全性的考虑,在电池包设计时,在这些部位增加加强筋来提升结构的刚度是十分必要的。 04 结果讨论 电池包结构轻量化设计多为轻质材料下结构的静动态特性优化,选用合适的轻量化材料对提升电池包的结构设计技术和轻量化水平具有重要意义和工程应用价值,能够实现箱体有效地减轻质量和延长整车的续驶里程。
通过总结不同品型电池包在结构设计、材料选用、静态特性和动态特性4个方面的性能参数,比较了满足4个方面要求的轻量化电池包用材料的服役性能,评估了不同材料的轻量化效果。主要结论如下:
(1)在同等质量下,铝合金电池包的体积更大,有利于空间内电池模组的优化排布;同等体积下,铝合金电池包的质量更轻,可以多配置同等质量的电池,增加续驶里程。
(2)钢铁材料用作电池包箱体材料,占据了较大比例。其中,DC01和Q235两种材料是应用最为广泛的普通钢;在铝合金中,Al6082-T6和Al6061-T6是两种使用较多的箱体材料,但使用量远不及钢铁材料广泛,其成本限制了大规模应用。不同系列铝合金材料的比强度均显著高于钢铁材料,铝合金的轻量化性能优异。
(3)在颠簸急转弯和颠簸紧急制动工况下,铝合金电池包的最大应力范围均低于钢铁材料的应力范围;铝合金电池包的安全系数均高于钢铁材料范围。铝合金电池包的应力集中小且安全系数高,服役性能更好。最大应力主要集中在下箱体吊耳、托架螺栓孔、底面以及侧围。
(4)随着电池包质量的增加,一阶模态频率存在下降的趋势,电池包过重会增大与路面激励共振的风险。铝合金电池包的一阶模态频率在28.22102.34Hz之间,高于钢铁材料的一阶模态频率范围30.22~58.13Hz,选用铝合金电池包可在实现轻量化的同时提高低阶模态频率。振型主要集中在上箱体中部、下箱体中部和侧围,所以通过在这些部位增加加强筋来提升结构的刚度十分必要。
(5)铝合金是安全合适的汽车轻量化材料,可在不降低电池包动静态特性要求的前提下有效减轻车身质量,延长续驶里程。此外,铝合金还具有质量/体积值低、比强度高、应力集中小且安全系数高、一阶模态频率高等方面的优势,但其成本限制了大规模应用。随着对长续驶纯电动汽车需求的增长,发展高性能低成本铝合金具有广阔的应用前景。 05 文章来源
李全,王俊升,王兵,刘鑫秀.纯电动汽车电池包轻量化设计综述[J].汽车工程学报,2022,12(04):431-445.
新能源汽车的快速发展带动了动力电池的高速增长。动力电池生产流程一般可以分为前段、中段和后段三个部分。其中,前段工序包括配料、搅拌、涂布、辊压、分切等,中段工序包括卷绕/叠片、封装、烘干、注液、封口、清洗等,后段主要为化成、分容、PACK等。材料方面主要有正负极材料,隔膜,电解液,集流体,电池包相关的结构胶,缓存,阻燃,隔热,外壳结构材料等材料。 为了更好促进行业人士交流,艾邦搭建有锂电池产业链上下游交流平台,覆盖全产业链,从主机厂,到电池包厂商,正负极材料,隔膜,铝塑膜等企业以及各个工艺过程中的设备厂商,欢迎申请加入。
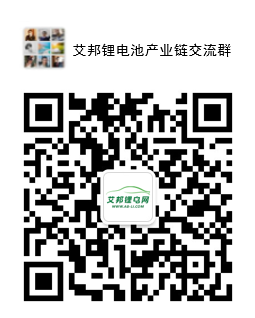
长按识别二维码关注公众号,点击下方菜单栏左侧“微信群”,申请加入群聊