马越:各位专家、各位企业界的同仁,各位朋友,大家好!今天给大家带来的报告题目是《高容负极的预锂和钠工艺开发》,前面报告已经讲到了硅碳负极设计以及石墨材料具体的各种产品类型的比较和一些产品构型上的设计。我的报告带来一点不一样的,从另外一个角度,有没有可能针对高容材料进行极片层面的改进,从而提升它的整体性能。
首先是背景,我简要讲一下,高比能的电池是支撑我国战略和民计民生的基础,随着单体电芯能量密度的提升,在电芯内多尺度的这样一个界面的稳定性,就变成了非常核心的挑战。我们设计高能量密度电芯的同时,同时还要兼顾其安全性,尤其是高温、低温的安全性和额定能量密度这些关键指标的同步提升,其实可以看到在一些电推进系统里面还是需要这种高功率的体系,在平流层无人机、边防的巡检,其实都对这种长续航、高温、低温的这种极端指标是有要求的,这就使得我们在设计高能量密度电池的同时需要兼顾多尺度的界面稳定性。
硅基负极研究的现状,我这边简要地讲一下。其实面临了一系列的科学问题和工程课题的技术挑战,其中包含科学问题,像今天很多报告都已经深入探讨了例如体积膨胀、界面和电极不稳定的问题,其中工程问题又包含了在放大工艺之中如何去进行合理产线的工艺匹配。在这样一个过程中,我们希望可以更加针对的像硅基负极这种高温材料它的失效机理,进而进行离子补偿,从而希望从另外一个方向,从极片层面看有没有可能对它的整体性能进行修饰和提升。
总结硅基负极问题的剖析,其实可以看到不仅是颗粒的这样一个粉化和脱落,界面形成的SEI,以及锂化合金、去合金过程中产生的不可逆络合相,其实最终的结果都是导致非常严重的离子消耗。其实我们更希望去看到这样一个离子消耗,究竟是由于什么样的一个过程来形成的,有没有可能针对这样一个离子消耗,针对性的去补充合适的锂,从而提升在电芯层面的循环效率。但是如何去实现在高能量密度电芯中精准的离子补偿,就变成了非常具有挑战性的一个关键难点。在这之中,我们就需要首先了解失效机理到底在哪一个部分,究竟是哪一个部分消耗了过多的锂离子,从而可以针对性的进行这样一个离子补偿。
再回顾现在已经有的一些预锂工艺的策略,其实我们可以看到像常规的比如说美国公司的SLMP,包括其他的化学理化方法,我们都是在负极的浆料中加入补锂的试剂,同时伴随着一些问题,包括在匀浆过程中会产生更多新的问题,例如匀浆分层,包括面密度做不上去等等,在工艺当中,有的公司或者有的科研机构尝试过程中都遇到了类似的问题。包括化学预锂,能够更加均匀地进行极片层面的补锂,同时带来一个问题,用的这些溶剂,包括一些预锂试剂,其实都是需要非常严格的入点的控制,才能把这些预锂试剂的作用更好地发挥出来。
这几类的预锂方法其实都集中地反馈了一些问题,例如我们补锂工艺的这样一个价格其实还是比较昂贵的,包括在匀浆过程中无法非常好的均匀分散,其次还有与极性溶剂的不兼容,加入预锂试剂混匀性太强,有可能把一些极性溶剂全部都还原了,从而产生更多不可逆的反应。
其实我们可以看看钠离子电池,今天也有很多报告讲了硬碳负极,但硬碳负极同样伴随着低首效的问题。那么在此过程中也有很多类的预钠化的工艺方法,钠锂电池负极利用率的提升策略除了对于本征的这样一个结构进行改进之外,无论是我们从一系列的科研报道和我们从工程化的探索当中,其实现在能够实现的上限库伦效率差不多在90%左右的状态,如果真正进行工程化放大的时候,10%的这样一个不可逆的容量损失,其实也是需要进一步在电池体系之中进行一定的离子补偿。
综上,我们看到预钠化的方法,前期也是进行了一些比较初步的,在科研层面上,很多报道,包括化学预钠,钠粉预钠,电化学预钠,以及直接的预钠方法,同样面临着像预锂同样的问题,我们如何精准地把这些离子放到电芯之中,产生失效的这些部分,从而提升它的循环性能,这是非常关键的基本科学和工程问题。
因此,我们的研发思路还是通过一个可以多场耦合原位相变表征的体系,大概是什么意思呢?就是我们把这个电池放在一个合适的台子上,去模拟它在真实服役状态下的工况,比如哪一个温度、什么样的磁场、什么样的压力,然后对它进行充放电。我们通过X射线,将它正负极变化进行分析,定制化地观察到到底它在发生容量损失的状态下,究竟是正极还是负极,发生了这种不可逆的相变。针对这样一个结果分析,从而再去进行精准的补锂,这就是我们进行这种功能开发和研究的一些思路。所以从这样一个角度,模拟电芯服役的条件,建立失效模型的数据库,再针对性地指导电芯的制成和精准化预锂化策略。
第一部分的报告集中在开发原位表征技术上,特别是它可以模拟电池在运行状态下是如何失效的。
首先我们将单层的软包体系,不同的电池构型的单层软包体系模拟乘一个小的软包体系,并且对它进行循环。X射线打穿正极负极以及所有的组件,再循环过程中就可以将正极负极的晶体结构进行非常细节的分析,对于它的晶体结构、缺陷、硬力等等,动态循环过程中,如何发生这样的一个失效过程,特别是在不同的应用条件下,在不同的温度下,不同的压力下,究竟正负极是如何发生这样一个失效的,这就是我们通过这台X射线衍射仪可以进行细节分析的过程。在这个过程中也可以反映出一系列的指标参数,包括晶体结构、缺陷,以及每一个晶胞,正负极如果是一个结晶相,有连续相变过程的话,可以反映到每一个晶胞的晶胞参数的变化过程,从而我们就可以有效地观察它的可逆性,循环的可逆性,是不是库伦效率能够接近于100%,如果发生失效的时候,究竟是正极还是负极发生了这样一个失效过程。
其次我们通过这样一个台子的设计,我们可以看到一系列设计,核心目的就是想模拟电池在真正循环过程中,到底是正极坏了,还是负极坏了,晶体结构发生了怎么样的变化。我们进行了光源跟检测器匹配性的设计,从而将这种软包电池在服役过程中、循环过程中发生的这样一个失效状态,进行了这样一个环境的模拟。在这样一个样品台之上,我们尽量模拟它在真正循环过程中的工况环境,从而去看到底这个电池体系是怎么坏了,我们设计的这样一个电池构型是否合理,NP比,电压的设计,是否能够合理地返回这样一个失效的过程。
这个过程中我们可以模拟一系列静态状态下自放电,包括自放电状态下晶体结构的变化,其次动态循环状态下,以及这种极端状态下,尤其包括高温低温和热失控、自放电等等,不同循环状态下,它如何失效的,就可以进行晶体结构上的精准解析,我们可以看到底是正极的离子利用率较低,还是负极的离子利用率较低,然后进行合理的离子补偿。
同时我们进行了一系列样品台的设计,包括毛细管样品台、高低温样品台、投射模式XRD,以及原位高温样品台。这个台子有什么用呢?可以稍微解释一下,比如像所有锂化过程,我们在做预锂化过程,以及正极材料最后一部分的锂化过程,我们可以精准地用这个台子找到到底是哪一个温度,正负0.1度这样精准的温度,发生了完全的这样一个锂化过程,也就大大节省了我们真正做工艺开发的时候,这样一个正交试验设计的过程,所以对产品开发还是非常有效的。
第二部分是我们利用第一部分的耦合场状态下的原位表征技术,指导硅碳负极预锂化的这样一个策略。我们虽然前期做了大量的硅碳材料的结构设计,但今天我想分享的是我们用了比较常规的硅碳复合材料,也是基于之前我们共同合作的功能项开发的,可以实现1000/克的硅碳负极。在这样一个极片层面上,我们进一步进行极片补锂,我们先是设计了一个可以进行导锂跟导电的层,在这样一个状态下的时候,从金属、锂铂、支撑层,以及最终的硅碳负极,堆叠在一起,施加3兆帕的堆叠应力,实现极片层面的极片应力。通过这样的过程,锂离子就传输到可以导锂导电的层,通过这样一个电压的梯度,传递到了最终我们需要预补锂的硅碳之中。并且我们可以发现,通过调节它的厚度,以及它的组份比例,我们对于它的离子导电率和电子导电率进行一个精准控制,包括它的力学强度,现在其实这边虽然演示的是1米长,其实已经可以实现10米长度的涂层,虽然它的拉伸强度还不足以支撑可以卷对卷去做的这样状态,其实对于我们做这种批量的软包体系其实已经可以匹配上了,并且有很好的柔性。
这样的预锂方法,我们可以发现,通过不同的接触时间,从6分钟、10分钟、15分钟等等不同的时间,它的首效就从传统的一千容量/克的硅碳,从77%一直持续提高,最终能够提升到100%,甚至超过100%。库伦效率进行有效的提高,并且我们用(英文)的一种方法去分析了界面层到底是哪些组份进行比较这样一个均匀的分布,可以发现缓冲层调控预锂化方法之后,生成了碳酸锂的这样一个结构,也就是意味着我们在压延预锂的过程中,就先形成SEI的这样一个过程,我们称之为比SEI这样一个组份结构,质量上会更好,更加可调控的这样一个组份设计,在化成之前就已经完成了。并且我们借助了原位SRD的方法,观察到在这样一个压延过程中,锂离子其实已经可以部分嵌入石墨结构里面,并且形成二阶的石墨拆层结构,晶态的硅也部分变成了无定形的锂硅合金。通过这样一个方法,可以更加均匀地实现至少微米尺度上对于含锂材料预补偿的过程。
通过这样的方法,我们将一千容量的硅碳,跟811匹配,并且装成了1.6的软包电池,发现补锂和没有补锂的过程中,性能的表现差别非常大,循环性能最终可以实现1000圈,还可以保持在90%以上的循环状态。值得注意的是,这是一个容量接近于1000的硅碳负极,跟811直接匹配的,也是相对来讲比较极端的能量密度,以及循环稳定性的这样一个工艺调控。
另外,值得注意的是这边的倍率性能也得到了有效提升,锂子补偿过程中,我们将颗粒与颗粒之间的粒子通道提前建立起来了,在循环过程中它的内阻其实是降低了,倍率性能也得到了一定提升。
但是这样的方法其实还是面临了一些问题,比如说我们还是要拿锂铂压延这样一个状态下,进行这样一个压延工艺。有没有可能开发出一种可以耐高湿度环境下的材料,在这个过程中,其实我们初步尝试了足水足氧的材料,并且跟高锂硅合金进行了一个复合,并且在硅基材料极片表面进行了一个涂覆。从同等硅材料来讲,在循环过程中就产生了这样一个极片膨胀,最后导致电极粉化。这样一个设计,我们可以看到从上到下有一个锂离子的浓度梯度,通过这样的浓度梯度,我们进行了一系列的模拟计算,发现这样的一个结构非常有利于极片一体化的设计,从而在循环过程中,力学分布也会更加合理、更加均匀,不会使得膨胀状态下产生电极粉化的过程。因此,在这样一个梯度模型过程中,我们就是把一个补锂层涂在了硅基负极的表面,从而实现了梯度锂化的模型和硬力变化的调控。这是我们初步做的一些工艺流程,但是现在这边已经有改进,我们用了更好的一个足水足氧的材料,录点(音)在负20的条件下,就可以尝试进行这样的一个离子补偿控制,但是它在合成环境下,还是需要非常精准的这样一个湿度控制。
在这个过程中,其实我们也看了它足水足氧的性能,在常规的这样一个材料下,会迅速地生成氢氧化锂,但是我们进行了工艺改进以后,它就不生成氢氧化锂,其实是可以跟811电池装配线的湿度环境有比较好的匹配性。并且长时间暴露在高湿度环境下的时候,质量没有提升,也就意味着没有吸水。所以因此我们是用可以进行空气稳定的离子预补偿工艺,实现了在高湿度环境下,这边几张图证明了湿度到60%的环境下,还可以发挥出接近于80%的离子补偿容量,从而实现硅碳负极的补偿。所以在装配的811跟硅碳负极的电芯之中,我们可以看到,首效其实就提升了88%左右,88基本上就是正极811的首效,因此我们把硅基负极做到了库伦效率100%,然后进行电池装配,最终可以实现循环1000圈,容量保持率大于80%的电芯设计。
我们进行了一些离子梯度的模拟,发现在涂覆的这样一个锂22硅5的表面之后,其实渐渐中间就会生成绿色的锂14硅6这样一个体系,而且它是自发形成的,这样一个离子预补偿工艺跟底下的硅,自己就建立了离子梯度的这样一个模型,从而更好实现离子补偿跟硬力模型协同的作用。
现在我们还做一个工艺,我们希望可以用干法电极进行锂子补偿工艺。它的好处是我们可以在非常高面密度负载状态下的时候,进行极片的制作,并且现在初步尝试,已经可以实现非常高黏附力和高负载条件下的这样一个极片制作,上限可以做到8毫安时/平方厘米,远远高于传统用湿法去做硅基负极的这样一个工艺,并且在这样的过程中,我们可以加入合适的离子补偿试剂,进行高库伦效率的硅基负极这样一个极片的制备。
这边就展示了我们初步的一些图。
另外我们把刚刚的离子预补偿工艺用在了硬碳负极上,前期我们做了一些初步探索,将软硬碳协同起来,进行孔结构的调控。早上很多报告也讲到了,需要对它的微结构,包括它的孔径进行非常精准的控制,所以一系列的控制,因为没有在工艺上花太多的时间,就是在一次批量10公斤级别的这样一个硬碳跟软碳复合起来的工艺当中,首效也就接近于80%,我们没有进行更加精细的细节探索。但是我们同样将这种钠离子的补偿工艺用在了这个体系上,同样是调了很多的力学模型,包括离子跟电子的调控。我们还通过一系列的表征发现钠离子补偿之后,它其实可以进到这样一个材料的体系之内,它在这种小的二次颗粒之间其实进行了更加好的钠离子的嵌入。
通过这样一个方法,相较于直接预钠化,它基本都在表面,但是通过这样一个过程,钠离子能更好地进入碳材料之中,甚至进行孔填充的这样一个状态。
同样也做了一系列的全电池模型的设计,这其实是一个600毫安时的软包电芯,叠了7层到8层的样子,库伦效率包括容量保持率,以及倍率性能都得到了有效提升,离子预补偿工艺其实在锂离子电池和钠离子电池,对于所有的高容负极来讲,都是非常非常有效的,只要我们能够把这样的离子补偿控制的够均匀,而且量也足够合适,将前期会发生失效的这部分机理,预先进行补偿。
另外我们其实基于前面的离子预补偿工艺,进行了一系列的工程端设计,就是通过这样一个单层软包电芯在不同体系下的失效模型,从而指导我们的电芯设计,先把它这样一个失效模型找出来,再进行离子预补偿,最终进行电芯模型设计。
这是我们前期跟合作的厂家进行了硅碳材料的工艺开发,也实现了一个量产的硅基负极材料。那么这个过程其实也是从2017年,从实验室合成一直到最终的量产阶段。今天我讲的主要是我们的离子预补偿工艺,所以这里省略掉。
另外和合作企业共同开发的硅碳负极,其实也有比较完整的容量范围,从低容量一直到它的母体还是1600的这样一个容量,可以进行跟石墨结构的掺混,这边我就不赘述了,因为前面很多报告都是讲相关的内容。
另外硅氧材料的开发,也是进行了相关的高比容高首效的材料设计。说到我们的工程应用,其实就是基于我们和合作厂家开发的硅碳和硅氧材料,结合离子预补偿工艺。这是我们一个军民融合示范项目,特别是将极端的高能量密度的体系,最终用到无人机之中,其实我们做的是单体的能量密度大于400瓦时/公斤,可以循环差不多150圈左右,是完成了一个从小批量的电芯试验、台架试验,到最终应用试飞,今天相信很多行业内的专家也看到了,发布的这种航空级电芯,可以达到500瓦时/公斤,其实也证明了硅基负极企业在高能量密度体系里面,它其实有机会实现安全性跟高能量密度体系的同步指标协调,核心就在于我们的电解液中间这样一个凝聚态,包括分子链端的设计,应该如何去设计。
我们还设计了一些阻燃的电芯,其中用到的是这种阻燃的电解质膜和凝胶状的材料,从而可以实现这样一个阻燃测试的一些应用示范。
我们课题组基于我们开发的课题组,主要就是原位表征的这样一个平台,尽可能研究它的失效机理分析,进而指导材料的开发,对于我们而言,在三航应用上的这种应用示范。
最后谢谢大家!
(以上内容根据大会现场速记整理,未经发言嘉宾本人审阅)
原文始发于微信公众号(石墨时讯):西北工业大学 马越 教授 《高容负极的预锂/钠工艺开发》
新能源汽车的快速发展带动了动力电池的高速增长。动力电池生产流程一般可以分为前段、中段和后段三个部分。其中,前段工序包括配料、搅拌、涂布、辊压、分切等,中段工序包括卷绕/叠片、封装、烘干、注液、封口、清洗等,后段主要为化成、分容、PACK等。材料方面主要有正负极材料,隔膜,电解液,集流体,电池包相关的结构胶,缓存,阻燃,隔热,外壳结构材料等材料。 为了更好促进行业人士交流,艾邦搭建有锂电池产业链上下游交流平台,覆盖全产业链,从主机厂,到电池包厂商,正负极材料,隔膜,铝塑膜等企业以及各个工艺过程中的设备厂商,欢迎申请加入。
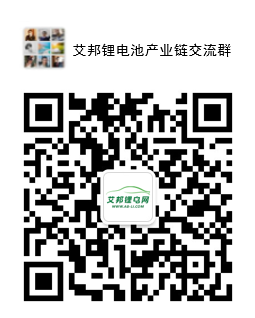
长按识别二维码关注公众号,点击下方菜单栏左侧“微信群”,申请加入群聊